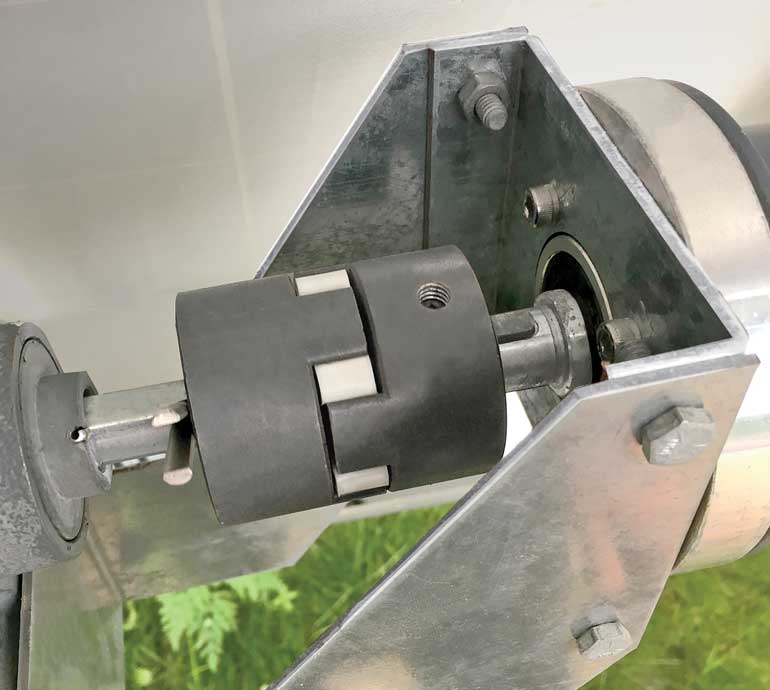
Reliable TB Wood’s L-Jaw couplings connect the drive motor to the driveshaft at the end of each row of PV modules.
Solar tracking system popularity has expanded as costs have come down and as more customers recognize the advantages compared to fixed-tilt systems for certain applications. RBI Solar is the latest well-recognized solar mounting system manufacturer for commercial and utility-scale projects to heed this market demand by debuting its Sunflower Single Axis Tracker.
“We provide single-source responsibility and peace of mind for EPC customers and project developers throughout the United States,” says Eric Oetjen P.E. at RBI Solar. “Developing this solar tracking system was a natural way for us to expand our product portfolio while providing a solution to an industry need.”
Designed to rotate PV modules on the East/West axis to maximize their energy production, the new system is aptly named since young sunflowers turn to face the sun as they track it across the sky.
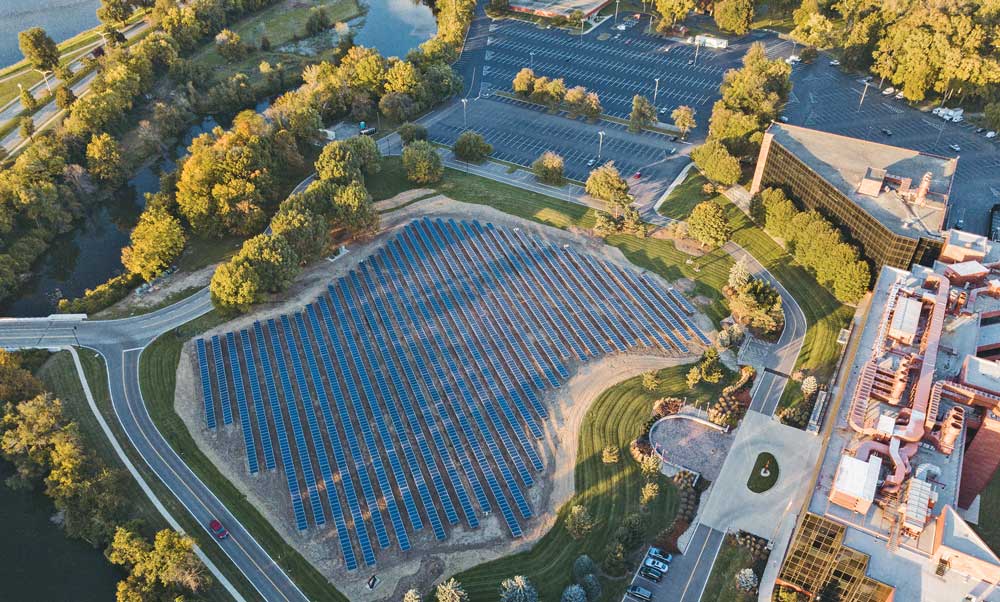
RBI Solar’s Sunflower Single Axis Tracker is designed to rotate PV modules on the East/West axis.
Alternative architecture
Most trackers in the marketplace rely on large motors and heavy steel members to rotate full rows of PV modules at a time. In large-scale installations, rows can be up to 400 ft long, containing as many as 120, 72-cell PV modules. The reason they need heavier steel vertical posts is because, as the large number of modules rotate, they create bending/torque stress. This stress is transferred and increases along the row from post to post.
To accommodate this stress, competitor systems often utilize increasingly larger post sizes as the posts get closer to the drive motor. For example, posts at one end of the row near the drive motor may be 6×9, while posts at the far end of the row may be 6×20.
The engineering team at RBI has developed a tabled (sectioned) system design that utilizes gearboxes. A gearbox is positioned at each post to transmit rotational torque into each foundation post instead of the motor shaft. This prevents accumulation of stresses to the motor. The result is a more load-balanced system that can drive long rows in a more cost-effective manner.
“These gearboxes provide two main advantages,” Oetjen says. “The design is non-back-drivable, so rotational stresses are absorbed at each post and not transmitted back to the motor. This allows us to use the same small post size throughout our entire system. This reduces cost and installation time.
“Secondly, because each row is made up of approximately 35-ft sections, large arrays can be installed over uneven terrain,” Oetjen continues. “Our Sunflower system allows each section of approximately 12 modules to be adjusted at each connection point to accommodate various topographic conditions. This is a major difference compared to systems that require relatively flat surfaces, since their module rows are made up of one continuous, rigid approximately 300-ft section.”
Small component with a big role
The Sunflower system, designed for commercial/utility-grade applications, required a reliable coupling solution to connect the drive motor to the drivetrain at the end of each row of PV modules. The RBI engineering team evaluated options and determined that an L-Jaw coupling was the most economical choice that met the system requirements.
During the tracking system development process, RBI began searching for a coupling source that not only offered the right coupling type and quality level but also convenient face-to-face support.
“Ultimately, we decided to work with TB Wood’s,” Oetjen says. “They were very cost-competitive. Plus, taking into account their high-quality product standards, superior customer service and convenient location, they were the ideal partner. The team at TB Wood’s was willing to work with us to customize the bore geometry of their L-Jaw coupling to provide a better connection to our driveshaft design.”
L-Jaw couplings are an excellent solution to connect two shafts and accommodate misalignment when ease of installation and low-cost are the primary considerations.
“These couplings operate with an elastomer element in compression, and they offer a fail safe’design, to a degree,” says John Smihal, product manager at TB Wood’s.
To meet the solar array application specifications and torque requirements, the modified LO95 L-Jaw couplings supplied use a Hytrel “spider” element with a torque capacity of 401 in.-lbs The couplings feature standard sintered steel hubs that are made in the U.S. If the elastomer legs of the spider fail, the coupling can still transmit torque through the hubs.
“We worked closely with RBI to revise our standard L-Jaw coupling bore design to accommodate their unique shaft geometry and provide a more secure hub-to-shaft connection,” Smihal says. “The TBW L-Jaw couplings provided the most flexibility, durability and consistent quality for our solar track system,” said Oetjen. “However, the overall interactions we had with TBW outweighed all other considerations. We were able to rely, with confidence, on their experienced and knowledgeable team as they provided engineering expertise and exceptional service and support, including fast responses, problem-solving skills and timely delivery.”
Several large Sunflower system installations have been completed and the TB Wood’s couplings continue to provide reliable, trouble-free performance.
— Solar Builder magazine
Leave a Reply
You must be logged in to post a comment.