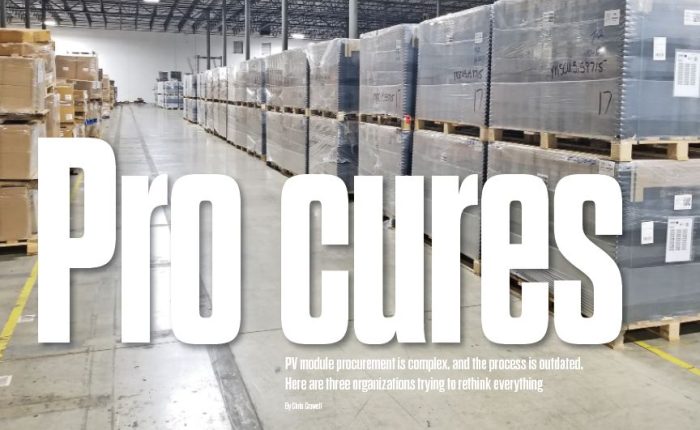
Solar module procurement has been precarious the last few years. The Section 201 tariffs of the Trump Administration. The Auxin petition to expand the bounds of the anti-dumping and countervailing duty (AD/CVD) tariffs. The allegations of forced labor in China’s Xinjiang province and the resulting Withhold Release Order (WRO) and Uyghur Forced Labor Prevention Act (UFLPA) sanctions on imports with components tied to that region.
Will the “normal” market return? Maybe. If it does, is that even a good thing? This disruption has been a great time for the U.S. solar industry to look in the mirror, and it has given solar businesses a chance to proactively pursue a new normal — one that’s more scalable and involves less risk and less inherent complexity for buyers.
In “Pro Cures,” in the Q1 edition of Solar Builder magazine, we looked at three different module procurement platforms that add some level of transparency, analysis or buying power that would be difficult for any one company to achieve on its own. Here is an excerpt from that feature. Check out the full “Pro Cures” article in the Q1 2023 edition of Solar Builder:
Solar Builder Instant Access
Get instant access to the digital edition of Solar Builder magazine.
And now for something completely different.
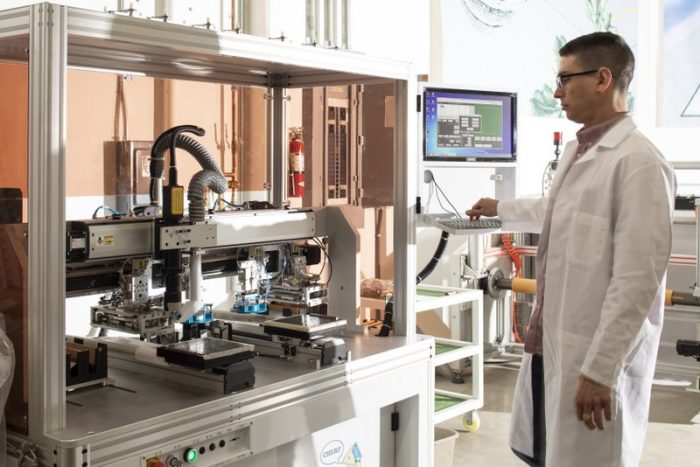
The reason the solar industry needs innovations like Inxeption and Anza is because of the complex global PV module supply chain. The position of CHERP Inc. is that all this solar module importing misses a much bigger opportunity to empower local communities. Even the new crop of billion-dollar U.S.-based facilities that will soon sell and ship modules domestically miss the mark.
CHERP Inc. is a nonprofit helping to build micro solar factories for nonprofit organizations in underserved communities across America through CHERP Solar Works. The goal is to jumpstart local 501c3 ownership of PV production inside local economies. Each modular solar module factory that produces PV panels for its area will then be part of a national Locally Grown Power solar factory network (trademarked by their technology partner idealPV LLC).
“We have an opportunity with solar to relocate the economic driving force of this production,” says Devon Hartman, president and CEO of CHERP, calling solar modules procured from outside a city “economic leakage.” “We can start a value chain to deploy energy inside local communities so that the profits can be recirculated as many times as possible inside the local economic unit.”
The first CHERP nonprofit solar module assembly factory prototype is now live in Pomona, Calif. Conversations are happening with 15 or so other cities around the country.
The facility in Pomona was helped by a $2.1 million budget allocation from the State of California along with another $1 million raised through donations and other grants and endowments. The Pomona factory will be able to produce 15 MW (50,000 modules) running at full capacity (three shifts). Additional factories will be able to produce 30 MW (100,000 modules).
Last we checked, CHERP was “installing the circuit boards on their modules and burning them in so they’re ready to go in for ETL testing,” according to Megan Anderson, director of admin and workforce development program manager at CHERP. “We just need to wait for idealPV to finish submitting the paperwork required before we drive the panels to Irvine for testing.” They anticipate starting production in the summer.
idealPV is receiving positive feedback from ETL about the numerous problems their technology solves. Kent Kernahan, Founder of idealPV, commented: “Our Spark Arresting Solar, First Responder Safe Solar, Fire Fail Safe, Short Circuit Foldback, Max Voltage and Max current safety features exceed the safety capabilities of any solar module submitted to ETL. Only idealPV modules measure temperature, voltage, and current. They are the first to actively regulate output maximums independent of the weather. These conclusions are the result of extensive design reviews and test planning with our ETL consultant.”
Another cool partnership is being explored with Seneca Solar, a solar developer and climate consultancy owned by the Seneca Nation in Western New York, to investigate the feasibility of building a CHERP solar factory on Seneca Nation lands.
“This opportunity fits our mission to profitably and equitably deliver innovative climate solutions that heal the Earth by investing in and building meaningful projects that benefit current and future generations,” says Hanna Sheridan, a member of the Seneca Nation, Bear Clan, and business operations manager for Seneca Solar. “We are excited by this possibility and our work to showcase the importance of renewable energy projects on Native lands.”
Do not mistake this plan as charity > ROI.
Hartman says the solar PV modules CHERP is producing are competitive in terms of LCOE (levelized cost of energy) and innovation. Kent Kernahan from idealPV, who invented the patented technology CHERP is using in their modules, has an additional six patents pending related to the module. Research and experiments conducted by Harvey Mudd College professors and students show the technology is “proven to have eliminated reverse bias,” which means no hot spots (and no bypass diodes). The assembly of the modules involves industry standard tooling and processes that require fewer and less expensive materials.
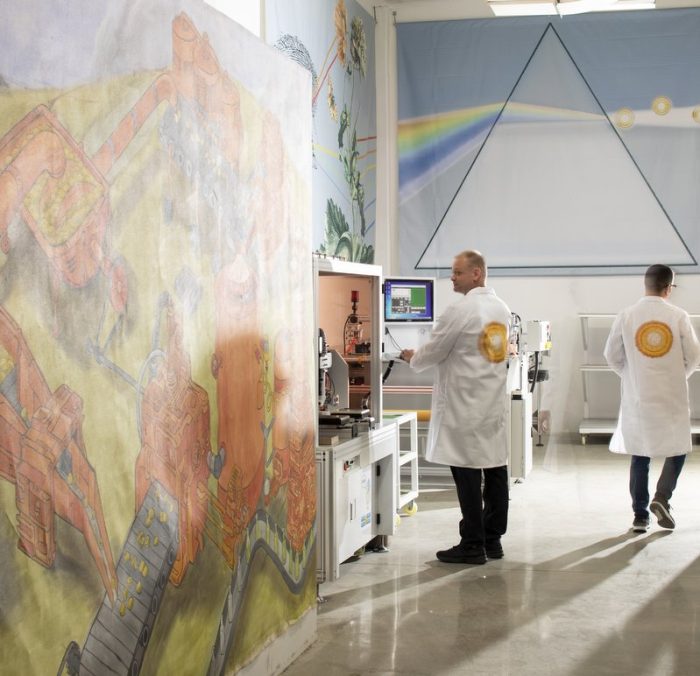
The 501c3 designation is perfect for local projects and is a big factor in that competitive LCOE. This way, CHERP factories can take advantage of “all the tools available to us in the American economy that helps us compete with the Chinese command economy where they just set prices from the top.”
“By the end of a year, we have zero capital expenses to amortize into product costs — zero CapEx,” Hartman explains. “Then, we can partner with third-party owner investment companies who have tax appetites and can take advantage of tax credits and depreciation along the lines of a standard PPA where investors take advantage of tax advantaged investment opportunities.”
That CapEx is typically part of the “economic leakage” of a solar project as capital for big purchase orders leaves the city, state and often country in which the solar panels are placed.
With CHERP’s model, a government can directly pay for the panels produced, or a PPA investor can get involved instead of only benefitting from kWh cost savings. And don’t forget all of those jobs, either. All in, a CHERP factory is a local investment in renewable energy that is paid back with local economic activity.
“Our goal is to create an economic vacuum, minimize economic leakage and generate economies from the ground up,” Hartman says.
He uses Goal 7A of LA County’s Sustainability Plan — to produce 10 GW of new distributed energy resources by 2045 — as an example. Generating this amount of energy would require about 30 million new solar modules. Achieving this goal using standard solar panels means a $5 billion investment that does not benefit the LA economy since a vast majority of all solar modules come from overseas.
If even just 15 factories get up and running, “we’d make 30 million solar modules, create thousands of direct and indirect jobs, and keep that $5 billion invested and circulating locally,” he says.
Unfortunately, solar cells are one source of “leakage” within CHERP’s model because there are no U.S.-based cell manufacturers to source from yet, but they will jump in line as soon as a U.S.-based cell facility comes online — or take advantage of a completely new solar cell altogether.
“We have a relationship with an MIT graduate named David Berney Needleman who is working on new cell technology that, if successful, would change the game for us,” Anderson says, referring to Leap Photovoltaics, which was a finalist in the 2022 American-Made Solar Prize competition. The Leap PV team is developing a silicon solar cell that uses silicon particles instead of traditional silicon wafers.
CHERP’s vision is its own leap, for sure, but one that cities and counties around the country should consider taking, especially those lamenting the loss of jobs from other long-standing energy industries, like coal or oil and gas. For those that are interested, CHERP has a business plan, a comprehensive sales and marketing plan, and potentially “new sources of funding that will help make it easier for communities who are interested get access to the funding needed to start one.”
Chris Crowell is the Editor-in-Chief of Solar Builder.
— Solar Builder magazine
Leave a Reply
You must be logged in to post a comment.