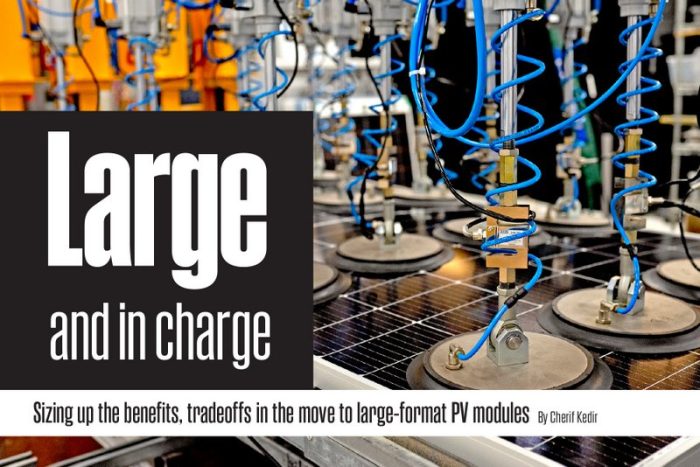
This is an excerpt from the Q2 2023 issue of Solar Builder magazine, written by Cherif Kedir, president and CEO at the Renewable Energy Test Center (RETC), an accredited testing laboratory for solar photovoltaic and energy storage products. Subscribe to Solar Builder magazine for free (print or digital) right here.
Lowering costs, improving performance, and increasing the speed of deployment are essential to the solar industry’s ability to compete with fossil fuel power sources. Our collective ability to drive costs out of the project value chain is one of the primary reasons solar accounted for 50% of all new electricity-generating capacity additions in the U.S. last year.
Today, one of the most promising opportunities for continued cost reductions, both at the module and system level, relates to developing and deploying large-format PV modules. The value proposition is so compelling that some industry analysts expect large-format modules to account for 90% of the utility market by 2025. Recently, large-format product adoption has started expanding beyond the utility sector into distributed generation (DG) markets.
In this article, I explore what is driving the industry-wide pivot to large-format PV modules. I also consider unique technical risks of these new products and recommend strategic risk mitigation approaches. In sharing these insights, my goal is not to recommend or vilify a specific product, technology, or manufacturer — rather, it is to empower you to identify and specify the best products and system designs for your unique applications.
Large-format benefits
The high-level benefits of large-format PV modules are easy to see. Larger wafers and cells — typically 182 mm (M10) or 210 mm (M12) square — facilitate larger form factor modules. These new modules are generally more than 2 m long and have capacity ratings ranging from 500 W to more than 800 W.
For an industry long accustomed to incremental module capacity improvements, super-sized PV modules represent a massive jump in module-level output power ratings. Year-over-year cell-efficiency increases typically result in output power gains of 10 W to 15 W annually. By comparison, the switch from a traditional M6 (166 mm square) wafer format to M10 or M12 wafers might increase the module-level output power by 100 W to 150 W.
The value proposition for large-format PV modules is multilayered.
- At the manufacturing level, large-format modules facilitate efficiencies of scale to drive down production costs.
- Further downstream, large-format modules promise additional cost-per-Watt savings, as handling fewer higher-capacity modules for the same plant capacity provides logistical efficiencies and drives down in-field labor costs.
- At the system level, large-format modules increase source-circuit power levels, enhance plant-level energy density and facilitate balance of system (BOS) savings.
Hongbin Fang, LONGi Solar’s director of product marketing, notes, “In the last couple of years, large-format modules have been an effective way to improve module power, achieve lower manufacturing cost, and help customers to reduce BOS cost. As a result, large-format modules have helped the industry accelerate the process of achieving a lower levelized cost of energy (LCOE).”
Large-format tradeoffs
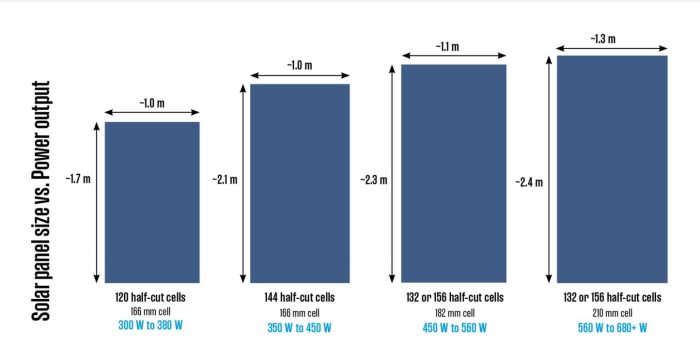
When evaluating large-format modules for specific projects and applications, bear in mind that upfront savings may come at a cost. Some risk and uncertainty are inherent to any new product or technology with limited field exposure. However, large-format modules also present some unique challenges.
From a structural point of view, large-format PV modules expose a larger module surface area to the same environmental stresses for a given location. All else being equal, larger modules are inherently subject to an increase in body deflection and torsion compared to smaller modules. As a result, the silicon cells in these modules are subject to increased mechanical stress and pressure. In practice, however, all else is not held equal as module surface area increases.
To counteract the 20% to 30% increase in module surface area, it is not uncommon for manufacturers to reduce glass and module frame thickness in an effort to control weight. This convergence of variables — characterized by heavier but thinner module glass, longer but lower-profile aluminum perimeter frames, and a larger surface area — invariably results in a weaker module.
RETC’s hail durability test data indicates that large modules with thinner front glass are less resilient to severe diameter hail than previous module designs. This vulnerability is partly a function of the fact that thinner glass has less cross-sectional area to absorb a shock without shattering. More critically, heat tempering requires a minimum glass thickness (≥3.2 mm). Many large-format bifacial modules have a 2.0 mm glass-on-2.0 mm glass package. This “heat-strengthened” glass is not as strong as tempered glass.
Large-format modules may also increase risks associated with accelerated performance degradation or long-term operating costs in high-wind areas or high-elevation locations with extreme snow loads. Elevated environmental stresses will tend to exacerbate deflection and torsion in large-format PV modules, increasing the potential for cell cracking. As cell cracks increase in severity, so does the risk of performance degradation, service life reduction and hotspots.
Meeting the challenge
Until large-format modules are a proven commodity in diverse environments and market sectors, project stakeholders must carefully assess these products based on the specific installation environment and highly accelerated life testing data. Moreover, the industry needs to ensure its testing protocols and sequences are adequate to capture potential failure modes and wearout mechanisms in modules subject to higher mechanical stresses, including heavy snow loads and dynamic wind effects.
“Higher power class modules are here to stay,” says Daniel Chang, senior director of solar product management at Qcells North America. “But these product innovations still need to withstand a 25- or 30-year project life in extreme environments. This is why beyond-certification testing in the laboratory is so important. By validating product designs via highly accelerated third-party testing, the industry is able to bring innovative products to market while ensuring long-term durability and performance.”
At the end of the day, the risks and rewards associated with large-format modules are not equitably distributed. For module manufacturers, the trend toward large-format modules is an opportunity to increase profit margins and differentiate themselves in the market. For developers and EPCs, this cost-saving opportunity may increase close rates and market share.
In the event that in-field reliability and performance suffer, host customers, insurance companies and financiers are likely the ones footing the bill. Therefore, these project stakeholders and their technical advisors must ask the right questions and review relevant testing data when qualifying large-format modules, especially for locations subject to extreme weather.
Super-sized in resi, C&I
The utility project sector is ideally suited for leveraging economies of scale. As such, module companies developed the first PV modules to integrate M10 and M12 cells with 1,500-volt ground-mounted applications in mind. Today, more and more manufacturers offer super-sized PV modules for distributed generation (DG) applications.
Especially in behind-the-meter rooftop applications, it is important to holistically evaluate the pros and cons of large-format products.
Product storage: For some manufacturers, the pivot to large-format module designs coincides with innovative packing configurations that optimize container utilization. In some cases, manufacturers palletize modules in a vertical format, which may necessitate warehouse compatibility upgrades. On the jobsite, pallets with a smaller base area and taller center of gravity may require special attention to prevent tipping. Pay attention to point load limits when staging low-slope rooftops.
Material handling: Large-format modules are incompatible with single-person handling, which may impact optimal crew size, workflow and jobsite safety. Bigger and heavier modules will increase crew member fatigue, potentially requiring additional rest and hydration breaks. In some cases, existing rooftop transportation practices will be incompatible with larger-format products. If so, consider investing in rooftop transport equipment that improves jobsite safety and project throughput. Pay attention to vehicle or trailer load limits during transportation.
Design flexibility: Bigger is not always better in space-constrained applications. On the one hand, high-power product designs reduce the module count for a given project capacity. On the other hand, large-area modules may limit array layout options. This challenge is especially true for rooftop projects with many obstructions.
BOS compatibility: Integrating large-format PV modules into DG applications may require different power electronics and racking components as compared to business-as-usual systems. Designers may not experience BOS compatibility problems with systems designed from scratch with high-power modules in mind. However, substituting large-format modules for conventional products may require re-engineering and procuring alternative products.
For more in-depth articles like this from our Q2 PV Market Guide, access the digital edition:
Solar Builder Instant Access Q2 2023
Get instant access to the digital edition of Solar Builder magazine.
— Solar Builder magazine
[source: https://solarbuildermag.com/featured/benefits-and-tradeoffs-of-large-format-pv-modules/]
Leave a Reply
You must be logged in to post a comment.