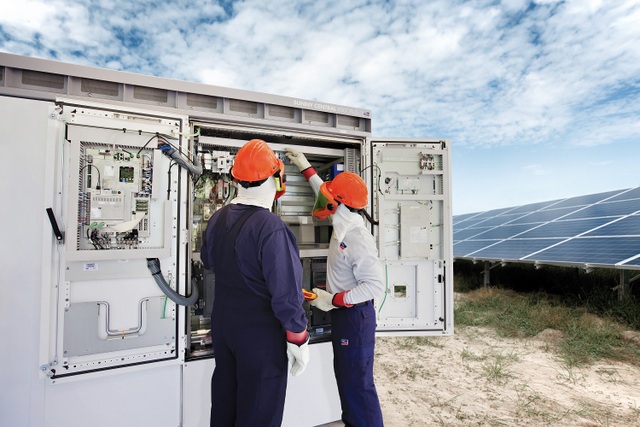
Photo of SMA O&M services,
In a post-Trump Tariff world, optimizing current portfolios is crucial, not just for each project to hit its targets, but to continue to prove solar as a worthy investment and distributed resource. Luckily, this is easy to accomplish with a well-thought out operations and maintenance (O&M) plan.
With more than a decade of hardcore O&M industry experience, there is a greater reservoir of institutional knowledge both out in the field and in plant operation management. For example, MaxGen is a U.S.-centric O&M provider focused on utility and C&I sites that manages a large team of licensed, professional technicians throughout the country, hitting about 5,000 different sites a year for corrective (CM) and preventive maintenance (PM). As part of its business model, the company will take over portfolios of assets to monitor — some of which are underperforming. According to Mark McLanahan, CEO of MaxGen, assets are usually underperforming because of one or more of these reasons:
The site is not in good physical condition because of poor vegetation management or erosion or general site management. Consider this a reminder to keep O&M in mind when designing a project because it is often the largest expense over the life of the project. “Handling stuff like vegetation management and module washing can be the biggest expense by far if you’re not careful,” McLanahan says.
Poor PM records, which often means PM hasn’t been done. “That’s a problem because you have to perform PM to maintain warranties of inverters, combiners and modules,” McLanahan says. “We have seen many cases where service to date is either not verified or there’s no record.”
This is where PowerFactors comes in handy. PowerFactors is an energy operations management software platform that MaxGen has been using since 2016 to integrate all the monitoring, alarm management, work order creation and management, dispatch and reporting for all the operations, and preventive and corrective maintenance tasks in its scope of work with its customers. Also, contract requirements can be programmed into the system. For example, Power Purchase Agreements in California often require instant notification of large drops in capacity and failure to do this will incur penalties. Auto-notifications can be routed to the right places in those events with the right rules plugged into the software. This enables fewer operators to manage more projects with greater complexity.
The site data acquisition system simply hasn’t been mapped properly, which undermines the data quality of the entire project and leads to maintenance misdirection. There’s an outage on inverter A; a dispatched technician heads to inverter B because it’s mapped as inverter A. The issue isn’t discovered, and so on. McLanahan estimates that MaxGen encounters this in 20 to 30 percent of the underperforming sites it takes over.
“It’s a data quality issue,” he says. “With solar, you have to study performance at the low level, not just the revenue meter, to make decisions on performance. You have to look at inverters or combiners or at the main circuit. If the mapping is no good, you’re wasting time.”
Once the site is remapped and the PM is up to date, annual maintenance and CM plans are put in place to build it back to baseline performance using better data. From there, more advanced decisions can be made. Data can be studied for factors such as ground coverage ratios, tracker angles, performance anomalies at the combiner level and similarity-based modeling to help identify additional opportunities. MaxGen has boosted a number of utility-scale projects 2 to 5 percent on the performance side using this systematic process.
“With consistency, you’ll see 1 to 3 percent improvement right off the bat just with low-hanging fruit,” McLanahan says. “Compare the combiners on a relative basis on performance and just look at last month. That sets the corrective maintenance for the next week. Once you have accomplished all the PM tasks, have good data access and capture the low hanging fruit, you can move up the lost energy priority list and tackle the things that are above the baseline to increase production and revenue even further.”
The true bottom line in PV system performance, from initial projections to 30 years in the future, is customer service. People need to make the correct assumptions, perform all O&M tasks correctly and use data analysis to their advantage while being as proactive as possible. As more data is gathered and algorithms are perfected, “trend events” will be the next frontier for improving performance.
“These don’t show up as a discrete one-time energy loss but as small events that happen continuously over time, and if you don’t look for them you won’t see them,” McLanahan says. So, maybe one inverter is coming on and offline in mere seconds. “If you look at the curve, you won’t see it, but if you look at the trend, there’s something wrong with that inverter, and it will likely break down at some point.”
That curve is a nice visual to end on. Just plan to stay ahead of it.
— Solar Builder magazine
Leave a Reply
You must be logged in to post a comment.