“We build with solar energy — our fabrication facility is powered by renewables. We really believe in it, but solar support structures are kind of a nuisance for me right now,” laughs Tony Worthen, VP of operations and product development at Kern Solar Structures, when giving me the rundown of the company and the services they offer. This was at Intersolar North America back in February, seemingly a lifetime ago — a simpler time, when people left their houses and gathered in places to have conversations. I swear it to be true.
The main reason Worthen joked that this is a “nuisance” for him is it’s such a small part of his gig. Kern Solar at the moment is a new kid on the block in the mounting and racking space and their products are just a small part of a structural steel fabricator known as Kern Steel Fabrication Inc. Kern Steel has more than 60 years of experience providing structural steel fabrication services to the global construction industry in support of projects from conventional steel buildings, rides at Disneyland, working platforms that service the aircraft of the U.S. Armed Forces and even the C&I and utility solar industry. Kern Steel has decades of experience building structures for the global energy industry, including geothermal, solar, nuclear and (hold your boos, please) the oil and gas industry. Bottom line is they specialize in building high quality structural steel solutions that last, which is why I was interested in hearing what they had to offer solar.
“We initially treated this fabrication work for the solar industry just like any other fabrication job,” Worthen notes. “By 2017, we had started to realize a pattern emerging with the types of designs being specified by solar developers. We felt that Kern Steel was uniquely positioned to leverage the principles of lean manufacturing and circular supply chains to launch and grow a division dedicated solely to supporting the solar industry.”
With Kern Solar Structures, Kern doesn’t just want to tack on the extra business and supply solar support structures for the solar market that exists in 2020. They believe there are some fatal flaws in how solar sites are currently being developed, priced and built, and they want to offer an alternative vision, informed by their decades of experience building for, yes, the oil and gas industry as well as the global construction industry. This perspective shows in its current mounting system offerings.
Learn from thine enemy
Kern Solar is hosting a webinar with us on May 27 to explain Integrated Project Delivery and how its carport solution can be installed in a week, becoming a profit center for solar contractors. Register to listen or download right here.
Solar right now reminds Worthen of the O&G industry of the early 20th century — just put things in the ground and let it go.
“Very little was understood about corrosion and service life and it resulted in an industry plagued with field failures and the decreased service life of assets,” he says. “A primary difference between the two industries is that you own a pipeline or well beyond the design life of the asset, and oil and gas producers are constantly working to extend the service life of that asset. Consider the Trans-Alaska Pipeline brought online in 1977 with an expected service life of 30 years.”
A pipeline is a lifetime asset, and its retirement is baked into its expenses (now, whether these oil and gas companies ever actually retire these assets is another mustache-twirling story).
“In oil and gas, it was easy to overdesign, and even be wasteful, when the price per barrel is high, but regardless of the price of energy, at least you own the pipeline and you own the risks associated with the operation of that asset,” Worthen says. “In solar, if the utility grade solar asset begins to fail, you just find a new investor. As an industry, shouldn’t we be building PV systems on solar support structures that can last for 50 years? Renewable energy shouldn’t mean that we renew the PV system or the solar support structure every 10 to 20 years.”
This disconnect between solar development norms and construction best practices is most apparent to Worthen when it comes to price per watt (PPW), which he considers an Achilles heel of the industry.
“In the construction industry, a building is priced per sq ft and raw materials are priced by weight or volume. We describe projects and systems in units of square feet and tons and price things accordingly,” he says. “A PPW is dynamic, a moving target — a bad target. Consider a good commercial grade PV module just 18 months ago with a power density of around 15 watts per sq ft. Today, that exact same PV module frame has a power density of 18 watts per sq ft. Interestingly, both modules require the same solar support structure and much of the same BOS.
“This attribution of risk is also off,” he continues, now on a roll. “The EPC thinks they need a low PPW, but then the EPC doesn’t own the risk over the life of the asset. So, the EPC could be motivated to select an inferior solar support structure at a lower PPW because it meets their performance warranty requirement of 1 to 5 years. But the asset owner or finance company may be unaware of the reduced service life that could negatively impact their financial model. It’s a cultural thing we’d like to change.”
Kern designs, manufactures and prices its products as 30+ year steel structures with 20 to 30 year coating systems — no lightweight purlins or thin gauge metals with 5 to 10 year finishes. The end result of the design is a solar carport that actually uses 12 percent less steel by weight, 25 percent fewer structural components and 66 percent less bolted field connections.
This often carries higher upfront material costs, but Worthen thinks that contractors can bake more of a profit into these jobs by doing the installation themselves from start to finish, and do so in as little as three to five days.
“Kern Solar Structures is a manufacturer of solar carport systems designed to empower the EPC to lead both the design and installation efforts of a project,” Worthen says. “While fixed costs relating to design and materials continue to be heavily driven by engineering, soft costs can be addressed and minimized by the EPC. By performing your own installation you can ensure the regulation of soft costs, especially labor. You can maintain more control over bids and project pricing.”
This system could be especially helpful for contractors needing to regain lost revenues after the coronavirus quarantine ends by cramming more quality built projects into their schedule in a shorter amount of time.
A galvanizing issue
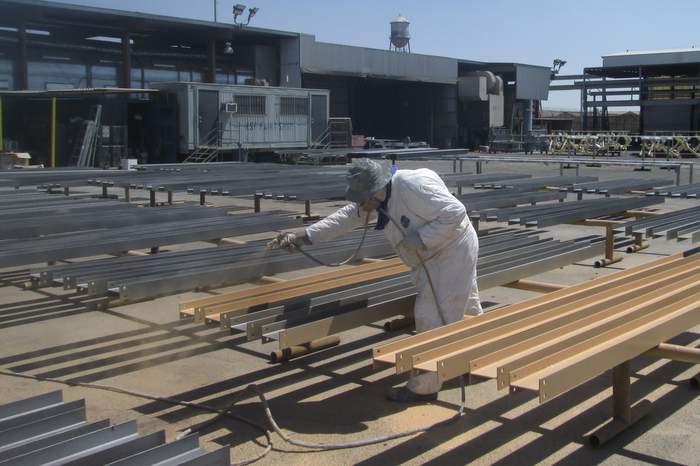
Kern’s approach is to characterize the soil conditions and then either go with a galvanized pile solution with a sacrificial coating if soil conditions permit or to choose from a variety of protective coatings such as its Envirolast 627 coating system, available on their X-Pile system.
The issue that Kern is most vocal about is installing solar support structures that are protected over the life of the asset, especially in harsh atmospheric or soil conditions. This first came to Worthen’s attention when Kern was asked to supply coated piles for a large utility grade project in the Imperial Valley of California. Historically, the solar developers of this area had been using galvanized steel piles to support their single-axis tracker systems — a fact that made his jaw hit the floor.
“The solar industry has an overdependence on galvanized coatings but generally fails to understand the limitations and appropriate application for this sacrificial coating system,” he says. “NACE [the National Association of Corrosion Engineers] in conjunction with the utility power transmission industry has well established practices for the application of a galvanized coating system, but the solar industry has elected to learn those lessons again on their own, and they have the potential to be some very expensive lessons. Galvanizing is not a one size fits all solution.”
Now, in some soils, galvanized steel is fine, but as mentioned it is a sacrificial coating, and it is imperative that the developer assess how that coating may affect the long term service life of the asset specific to each site’s soil conditions. All soils are corrosive to one degree or another. What makes soil corrosive? The American Galvanizing Association (AGA) says a soil’s moisture content, pH, aeration, resistivity and chloride concentration are the most important factors in the service life of galvanized piling.
Kern’s approach is to characterize the soil conditions and then either go with a galvanized pile solution with a sacrificial coating if soil conditions permit or to choose from a variety of protective coatings such as its Envirolast 627 coating system, available on their X-Pile system. The coatings are designed and tested to withstand the abuse that will be inflicted on them during installation, and Kern expects the service life for these coating system to extend well past 30 years with proper maintenance and inspection.
“The tools published by the AGA characterizing the service life of galvanized steel articles in high moisture soils (basically anywhere with an average rainfall greater than 10 inches per year) indicates that galvanized coatings should be used with prudence,” Worthen says. “Especially when you realize that a galvanized coating is typically 3 to 4 mils thick on structural steel (limited to 5 mils due to adhesion) or just 0.2 to 0.25 mils on cold rolled steel. The solar developer and especially the finance company holding the risk should both be concerned and make fully informed, experienced-based decisions.”
Depending on how moved you were by the price-per-watt critique, you might not care about this corrosion issue for a 20-year asset either, but here’s one last fun fact: zinc is classified as a heavy metal and has regulatory limits imposed and monitored by the EPA Clean Water Act. Thus, why Worthen hurt his jaw on the floor earlier.
Since galvanizing is a sacrificial coating, it will continue to sacrifice itself in the form of zinc oxide (which is water soluble) over its service life. Added together, there could be unknown ramifications. Many ports within the state of Washington, for example, are seeing increasing and alarming concentrations of zinc in the storm water runoffs that are being attributed to the dependency of zinc coatings on industrial equipment, piping, structures, roofing and fencing within those industrial facilities (and yes, there might be a galvanized solar support structure in that mix as well).
Solar is rightfully touted for its ability to reclaim brownfields, landfills and otherwise unusable spaces made so by human activity. So, it would definitely not be cool if solar projects going into the ground today had a similar negative impact on the environment after two decades — a bunch of near-busted, decommissioned structures left in a now heavy metal-contaminated plot of land.
I left my chat with Worthen thinking the solar industry could learn construction best practices from oil and gas, while also being careful to not replicate some of its worst practices. To build something much better, that lasts.
— Solar Builder magazine
Leave a Reply
You must be logged in to post a comment.