The traditional method of producing biodiesel involves a chemical reaction of an oil feedstock and catalysts like potassium hydroxide and sulfuric acid. Handling these caustic chemicals is dangerous, and production technicians must wear protective gear at all times during the fuel-making process. A recent breakthrough by Pittsboro, N.C.-based Piedmont Biofuels could change this process, however.
The company has launched commercial production of biodiesel employing a proprietary enzyme catalysis process that it says uses no chemicals and produces no waste. The announcement marks the first time this process has been used in the U.S. We recently spoke with Piedmont Biofuels’ co-founder and research director Rachel Burton, who leads the company’s research division, about what this company is doing to make biofuels a greener type of clean energy.

image via Piedmont Biofuels
According to Burton, the new process involves two enzymes, which both eliminate waste from either side of the biodiesel reaction. The first one replaces potassium hydroxide and “gets rid of the soap”—a pesky byproduct of traditional biodiesel production. The second one, which has been the focus of Piedmont’s recent research, eliminates the need for sulfuric acid by pre-treating the feedstock with an enzyme called Candida Antarctica Lipase B (CALB). This process, called Fatty Acid Esterfication using Enzymes, or “FAeSTER,” enables biodiesel producers to make zero-waste fuel from low-quality feedstocks like “yellow grease” (used cooking oil) and “brown grease” (grease that comes out of sewers and restaurant traps).
“These feedstocks are generally considered too degraded to use economically on a commercial scale,” Burton said. “The enzyme catalysts can also be reused—meaning that [producers] can make multiple batches of fuel from the same batch of enzymes.” Another major benefit is that enzyme catalysis is a much safer production method for the people involved in biodiesel production. “Now, when I make a batch [of biodiesel], I don’t even have to suit up,” Burton said. “It smells like I’m making beer. And, when I spill some on me, it doesn’t burn a hole in my skin.” (ouch!)
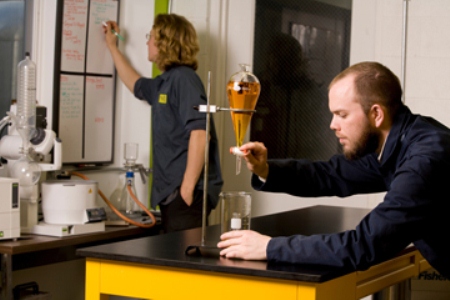
image via the Abundance Foundation
The announcement is the culmination of four years of research and collaboration with global enzyme producer Novozymes. Recently, this work has been supported by a Small Business Innovation and Research (SBIR) grant from the U.S. Department of Energy, and a partnership with the Clean Energy Alliance (CEA).
[source: http://feedproxy.google.com/~r/Earthtechling/~3/zyeGLJ-Hle0/]
Leave a Reply
You must be logged in to post a comment.