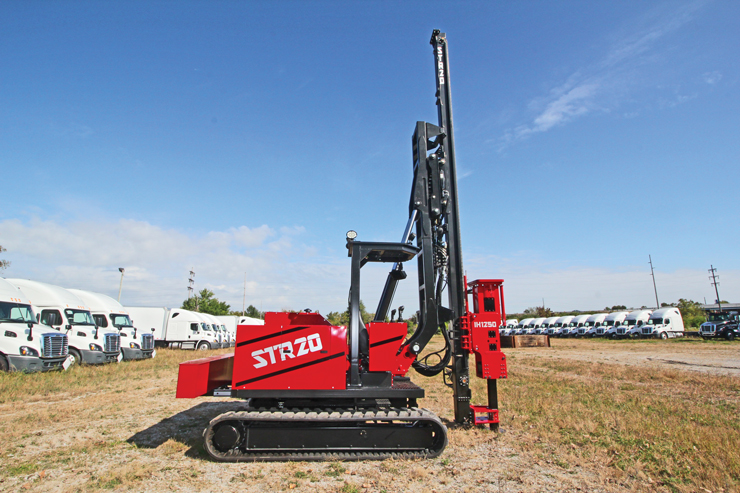
Hercules’ STR20
Before driving your piles into the ground, you have one huge decision that could be the key to delivering the project on time, on budget and possibly at a reduced cost: What machine will be driving those piles?
The brute force of a hammer might not be the one-size-fits-all tool required for the various terrains found on the solar jobsite. Plus, the beams typically being driven into the ground for a solar job are more fragile than beams in more typical pile-driving applications.
“Location and the plumbness of the materials are more important than in conventional pile driving,” says Tom Dame, national sales manager for Hercules Machinery Corp.
There’s also the wide variety of soil conditions that may require different approaches. The impact hammer is the most widely used application for this type of job, but an impact hammer isn’t ideal in all conditions. A good geotechnical report will indicate what tool is needed, but, maybe because of the quick turnaround world we live in today, Dame says a lot of the solar jobs he sees do not have geotechnical reports.
“If they had a soil or geotechnical report before it started, we could give good advice on which machine would work best, but the industry thought seems to be go out with the impact hammer because they are comfortable with it, and then if that fails try plan B,” he says. “Compared to other poling industry projects, the lack of the geotech testing really puts a lot of these guys between a rock and hard place because going out and trying to drive a beam into an unknown soil works eight out of 10 times, but for the other two times, no one has a plan B.”
Luckily, pile-driving equipment is now available on the market that specifically caters to the nuances of a large-scale solar project. Let’s look at some equipment features that will make Plan A the only plan you need.
Go Self-Contained
First off, go with a self-contained machine. Attachments added to a standard excavator have been phased out.
Auto-controls
Understand the controls that will vastly improve your speed, efficiency and accuracy, such as auto-level and auto-plumb.
Example: Both Hercules’ STR20 and Vermeer’s PD10 have auto-plumb control, which automatically orients the mast of the machine perpendicular to the ground. The auto-plumb also has a laser receiver option, which allows the pile-driving process to stop — without operator involvement — once the pile driver reaches the set point.
“This eliminates the operator guesswork and reduces the effort needed to install the post at the predetermined height — helping to minimize installation time,” says Jon Kuyers, senior global product manager for Vermeer.
RELATED: The value of a team approach to fixed-tilt ground-mount projects
GPS system
Some machines now come equipped with GPS systems that allow operators to upload predetermined project plans to help reduce surveying time and install piles at the correct location, depth and angle.
As Dame explains it on the HMC STR20 machine: “Once the operator gets there, one button moves the machine in and out, left and right and drives the pile down and shuts off at height. Once the machine gets close, everything else takes over and the machine does it.”
On one recent project that used a GPS-equipped machine from Hercules for surveying, the customer estimated $3 million in savings.
Remote operation
On machines with a remote control, like Vermeer’s PD10, the operator has access to the same functionalities as if they were sitting in the operator’s seat. This allows the operator to prepare the next post while the PD10 finishes driving the previous post into the ground, adding in another layer of productivity.
Like a manufacturing process, the PD10 needs to be “fed” posts to keep the project moving, so it helps when contractors streamline the post-delivery process in order to minimize the required movements and setup time between each post.
Mast and machine movement
A machine with left and right mast movement — without needing to move the tracks — can increase installation speed because the operator is required to perform fewer precise manual moves of the machine. Also, Dame notes that using an excavator that moves in an arc isn’t that helpful when trying to drive in a grid pattern.
Reliability
One of the biggest hurdles for a solar project is cost. Many solar jobs have very short timelines, so up-time and productivity are key factors in the decision-making process. Contractors need reliable equipment that can drive posts in quickly and accurately to produce a quality solar array. Most carriers should have a great lifespan, so there is no reason to wear one out other than general maintenance.
Pile length
Soil conditions will dictate what is needed, but the industry average is 14 to 16 ft. But again, how many average, routine jobs have you been a part of? Some situations will call for 19-ft piles or more. The HMC STR20 is capable of going to a 24-ft depth.
Attachment flexibility
This goes back to the ground condition considerations. The standard tool is an impact hammer, but this is not always the best solution. Other machine attachments you should have at the ready include a vibratory driver extractor (vibrates the pile into the ground or can extract it) and an auger drive (for drilling or screwing a helical anchor).
“We’re doing a job now in Utah where they drove a few hundred piles and then the engineering staff said they couldn’t get them down far enough, so they had to pull them all and needed to do them a different way,” Dame says. “Even on the job that the 6×9 [pile] is common on, they might drive 5,000 of those and then there are 1,000 6x12s, 100 6x15s, and then the corner posts are different. Having those multiple sections built into the drive cap in a universal base on there helps because with just a few bolts you can drive all of those piles.”
Chris Crowell is the managing editor of Solar Builder.
— Solar Builder magazine
[source: http://solarbuildermag.com/news/what-to-look-for-in-your-next-pile-driving-machine/]
Leave a Reply
You must be logged in to post a comment.