Youngstown, Ohio, is that quintessential rust belt city that boomed and busted right along with American manufacturing. But not all of those jobs skipped town. One staple in the area to this day is Northern States Metals. Founded in 1972, the company began developing aluminum-extruded industrial products and has served various industries (medical, military, automotive, etc.) for decades. The company thrives on helping customers devise their plans and then actually fulfills that vision, and it does this by keeping the key components — manufacturing and engineering — in-house, by way of American manufacturing and a team of engineers.
In 1997, Northern States felt the need to diversify further and enter this new, hip industry called “solar.” It started by manufacturing frames for panels, which led to the development of aluminum solar mounting clamps in 2008.
All of this leads up to the official creation of Solar FlexRack in 2009. We took the trip down I-76 from our offices near Cleveland to see it all for ourselves. The 100,000-sq-ft plant is impressive, housing the capability to supply aluminum extrusions from the lineal form to a fully fabricated and finished assembly. And like the company that birthed it, Solar FlexRack prides itself on both manufacturing better solutions (in the US of A) and providing in-house expertise.
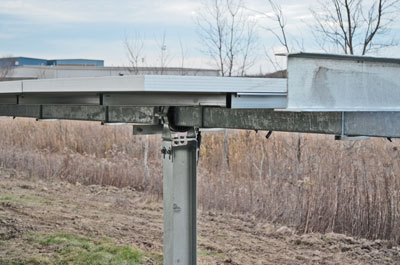
Onsite at the HQ, we also got a first-hand look at the brand-new, next-generation tracker system, TDP Turnkey Trackers
On the manufacturing side: Its FlexRack Series B ballasted ground-mount system was created to solve cumbersome shipping and time-consuming install issues by coming as a flat sheet that folds into place, requiring fewer components, fasteners and overall material.
“Our new ballasted ground-mount solution continues our ongoing drive toward more cost savings for installers and a better ROI for developers,” says CEO Tom Meola. “Our flexible racking systems solve the problems that come with difficult, uneven terrain, and this new ground-mount solution helps reduce the costs when ballasted ground mount systems are required because of soil conditions.”
RELATED: New single-axis tracker, turnkey service launched by Solar FlexRack
On the expertise front, Solar FlexRack is charging into the services revolution. The company employs a team of project managers and structural and mechanical engineers that can jump in during any phase of development to provide guidance on pull testing, foundation design, geotechnical design, installation, field support and maintenance.
And as Meola says, these services are more than an added layer of value. Companies that combine both the equipment for an install as well as the planning and engineering provide a real value that pushes the industry forward. Further, Solar FlexRack ties in its Certified Installer Program — hand-selected installers that meet certain standards — so that the company can be assured everything will be executed as planned and is capable of offering a full turnkey installation. Think of this streamlined product/services/installation bundle as you would the Series B ground-mount — fewer components, faster turn-times and simpler execution.
Onsite at the HQ, we also got a first-hand look at the brand-new, next-generation tracker system, TDP Turnkey Trackers. Solar FlexRack originally acquired the Opel technology for a single-axis tracker and completely redesigned it to achieve a lower overall balance of system cost. What sets the new tracking solution apart is its updated tracking technology bundled with a full suite of services and support for commercial and utility-scale solar customers.
The TDP Turnkey Tracker offers the lowest total cost solution by providing the only tracker in the industry that includes full design, installation, commissioning and support services bundled in one contract.
RELATED: Enjoy this exclusive video of the new FlexRack Series B, two-support rack system
The TDP Tracker has a flexible design that allows for close packing on odd-shaped lots and maximizes land usage due to its distributed design, requiring no welding, drilling, special tools or complicated jigs. Another key feature of the TDP tracker is the reliability and reduced maintenance offered by using industry proven parts that require no annual maintenance.
Service, support and trackers — this is the way of the world in 2016 and likely beyond.
— Solar Builder magazine
[source: http://solarbuildermag.com/news/solar-flexrack-in-house-manufacturing-engineering/]
Leave a Reply
You must be logged in to post a comment.