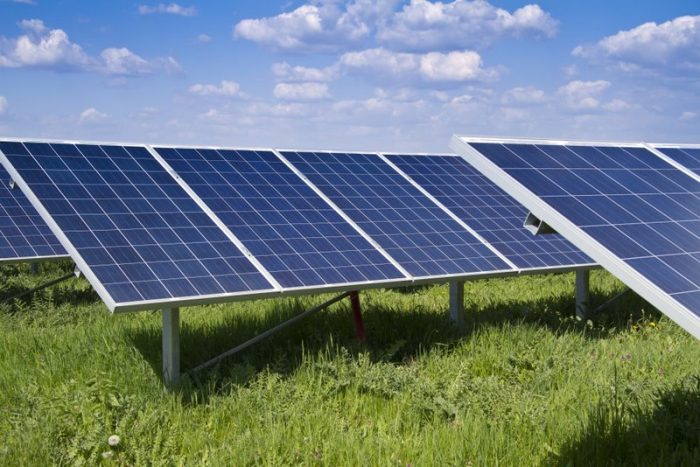
The PV connector is a solar component category still in need of innovation. The emergence of 1.5 Kv PV systems is a major industry trend that offers efficiency improvements and potential system cost reduction. However, the transition from 1.0 Kv to 1.5 Kv systems is also leading to more-stringent performance and safety standards for all components.
Chemical company SABIC recently announced a polycarbonate (PC)-based copolymer resin they say is well-suited for photovoltaic (PV) connector bodies, that meets stricter performance and regulatory requirements for emerging 1.5 Kv solar systems.
The main requirement is high CTI performance (UL PLC0 and IEC MG 1) to withstand 1,500 system volts without breaking down. Other properties are also critical, including ductility under exposure to very cold outdoor temperatures.
“To help photovoltaic customers keep pace with industry trends, particularly the move from 1.0 to 1.5 kilovolt systems, SABIC is proactively developing novel, higher-performance materials,” said Joshua Chiaw, Director, Business Management, LNP & NORYL, SABIC. “Our next-generation LNP EXL9334P resin grade, which meets stringent international standards for 1.5 kilovolt components, can facilitate adoption of this efficient, cost-effective technology. In addition to addressing changing industry requirements, this new material supports our sustainability strategy by helping to promote greater use of renewable solar energy.”
The new LNP EXL9334P copolymer resin achieves the highest comparative tracking index (CTI) level (UL PLC0) and IEC as Material Group 1 (IEC MG 1). It also delivers low-temperature ductility, good dimension stability, excellent heat resistance, good durability and weather resistance and flame retardance.
With high performance across all key properties, this specialty resin surpasses competitive materials such as glass-reinforced nylon, polyphenylene ether (PPE) and standard PC. Customers could also benefit from the cost-effective design flexibility and processing efficiency of this injection-molding thermoplastic.
In addition to achieving a high CTI (UL PLC0 and IEC MG 1), the SABIC material provides low-temperature impact down to -40°C, good weatherability (UL 746C f1 listing) and good dimensional stability. This new product also meets the UL94 V0 standard for flame retardance at 1.2mm and delivers long-term heat resistance.
“Developing a flame-retardant copolymer that could achieve the highest CTI level was difficult, but our experts were up to the challenge,” said Jenny Wang, Director, Formulation and Application, APAC, SABIC. “The SABIC team combined innovative thinking with technical expertise and successfully developed LNP EXL9334P resin, which meets the most demanding requirements across the board. Our efforts have been validated by customers during material trials. They are happy with its properties, particularly its signature impact resistance at extremely cold temperatures, which help solve their problems. We’ll continue to work on new solutions to support the high growth and new technology of the solar photovoltaic industry.”
— Solar Builder magazine
Leave a Reply
You must be logged in to post a comment.