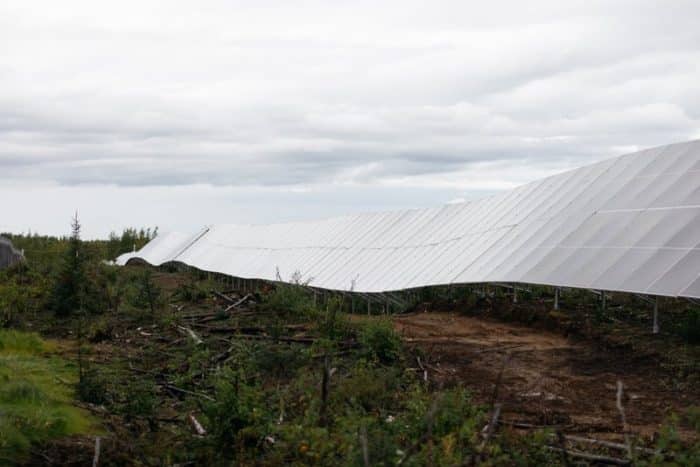
Over the last year and half, the Inflation Reduction Act (IRA) has built a bedrock of optimism for companies in the domestic solar industry. President Biden’s climate law has released billions of dollars of subsidies and encouraged new innovations and technologies, all while advancing the deployment of renewables. Fueled by the IRA, the utility-scale solar industry is indeed expanding at a rapid pace. According to SEIA, there are now more than 155 gigawatts (GW) of solar capacity installed nationwide. Wood Mackenzie forecasts that the total of new utility-scale installations will reach 172 GWdc between 2023 and 2028.
That being said, there are many complexities involved in utility-scale solar that require a great deal of expertise and experience. The lack of harmonized and industry-specific standards also contributes to the issues. In many instances, a ‘close enough’ substitute for standards is often applied. In solar cabling, for example, engineers have had to rely on electrical codes that are not relevant to current utility scale solar designs, as I outlined in my contributed article this past June.
At AWM, we offer a range of products and services, from cable management systems (CMS) to string level wire management and solar connector lockouts, designed for utility-scale solar installations. We know that each project is unique, and each varies state to state given topography, weather and selected components. For these reasons, we feel it is important that those involved in project development approach their sites with two key aspects in mind:
- Early collaboration to identify ways to build efficiencies into project development as well as to solve challenging terrain and geography challenges
- A “rapid response” mindset during the course of construction to help mitigate risks, reduce costs, and ensure developers meet project deadlines
Here are some advantages we’ve identified when integrating these two aspects into projects and partnerships:
Project-specific analysis that reduces costs. Often, blanket guidance is not adequate for the wide varieties of geographies that solar projects are developed in. Instead, require project-specific guidance, considering geographical-specific constraints to optimize items such as post length and mounting locations.
A solar CMS, for example, is extremely nuanced. It represents the intersection of several different engineering disciplines—civil, mechanical, electrical—so involving engineering professionals with years of experience, as early as possible, is crucial.
Sophisticated structural calculations will help EPCs save on steel costs when flood plains are restrictive, for instance, and allow the engineers to design the piles within the exact requirements needed. In addition, the versatile beam rod lengths let PV engineers allow for flexibility when designing post lengths and the solar CMS.
Installation guidance decreases risks. Detailed installation instructions for all eBOS products provides a lot of value. Example: Detailed guidance for string wire management helps mitigate catastrophic issues that are commonplace in this area.
For instance, a customer came to us at AWM during the golden row installation for assistance, and we were able to quickly identify the root cause and provide guidance to approach the golden row installation in a more efficient manner. Our guidance is tailored for each project, which helps improve installation practices and reduces risk within the rest of the project design.
Rapid response mindset ensures EPCs meet deadlines. Site nuances can require testing products for specific situations that arise during the course of construction. One example of this is a project where we faced extreme terrain grades. Testing the messenger cable angle in our advanced reliability lab allowed the project to move forward quickly and avoided massive remediation work.
Scenario evaluation solves weather-challenged sites. This doesn’t fall into the typical guidance, but there is good reason to seek it out. Alaska’s largest solar farm, built by Renewable Independent Power Producers (RIPP), is a good example of this. RIPP needed to maintain full access to remove snow in the winter with snowblowers, so the electric cables had to be placed 14 feet in the air. We evaluated the loads that were required, then worked closely with RIPP to develop a customized above-ground wire strategy.
Cable routing guidance also lowers costs. During review, have engineers look for value-engineering opportunities, such as optimal cable routing to reduce installation costs and improve site access. Opportunities to reduce cable size or cable length can result in documented cost reductions as high as 80% of the cable management system.
Scott Rand is chief executive officer and a founding member of Affordable Wire Management (AWM). AWM’s product line includes Arden Messenger Cable Hangers, Bonsai Module Cable Hangers and the Solar LOTO lock-out offering. AWM’s solar cable management systems (CMS) are the preferred choice for top-ranked EPCs in North America. For more information, please email us at sales@affordablewm.com, or visit us on the web at: https://affordablewm.com/
— Solar Builder magazine
Leave a Reply
You must be logged in to post a comment.