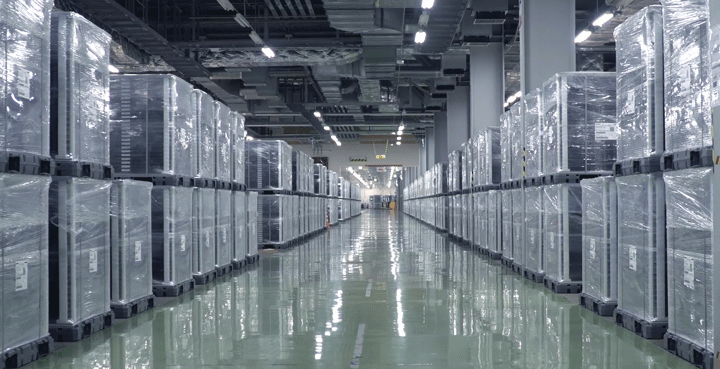
Solar Frontier’s 900 MW plant in Japan provided the scale needed to improve pricing.
A narrative has formed around thin-film PV modules that doesn’t totally match the reality. Initially neck and neck with crystalline silicon as the solar industry grew in the ‘90s, some high-profile big bets, headlined by Solyndra, did not pay off. We won’t rehash that old territory, but where previous technology and business plans faltered, the thin-film companies of today have refined and improved.
Scale to Success
One problem with past attempts at thin-film was scale. No thin-film manufacturers could really get there.
“Crystalline can be scaled by throwing labor at it. This is different,” says Charles Pimentel, CEO of Solar Frontier. “Unless you can do that [achieve scale], you can’t succeed at thin film. The upfront investment is too large, but once there, and you amortize that across volume, it takes substantially less from a resource and energy standpoint to manufacture the modules.”
Two of the bigger names in thin-film today do not have scale to worry about. First Solar, one of the largest solar companies in the world, has largely kept its CdTe panel technology to itself as it deployed gigawatts across the country in massive utility-scale projects. At Solar Power International this year, word spread around the show floor that the company was going to begin marketing its modules for distribution beyond its doors.
Solar Frontier and its CIGS modules seem poised to make just as large of a push. The company’s solar research and development dates back to the ‘70s, when it was just a small part of its parent company Showa Shell. In 2010, Solar Frontier started construction on a third plant that would significantly alter the trajectory of its technology — a 900-MW plant in Japan. This provided the massive scale needed to improve pricing. The company has achieved 4 GW of shipments globally.
But maybe more significantly, in 2015, the company completed its fourth factory, a smaller 150-MW line in Japan that is considerably more efficient than its other lines, applying years of learning from those other factories.
“The tack time has been reduced by 30 percent,” Pimentel says. “The efficiency has gone up considerably as well. All of that will net out to a reduction of cost in manufacturing of about 20 percent at full production.”
The plan is to take that improved process, scale it up and sprinkle additional facilities around the globe. They have a MOU with the state of New York right now to investigate the feasibility of a factory in its new solar region, for example.
RELATED: PERC Up: Boviet Solar tells us how it will provide high efficiency modules at a low cost
Thin-film efficiency
At a glance, thin-film can be dismissed because of its lower starting efficiency, but no solar panel value can be measured at a glance. For Solar Frontier, that glance is getting better all of the time. The company hit 22.3 percent cell efficiency recently, a CIGS record. Pimentel reminds us that most solar panel efficiency nameplate ratings are produced in a lab, under ideal conditions — conditions that are rarely seen in the real world over the life of a system.
The intrinsic value of any solar project always comes back to levelized cost of energy. Cell temperatures are always much higher than standard temperature conditions, so that initial, ideal efficiency is impacted by its intrinsic temperature coefficient. As the temperature rises, the real efficiency begins to shift. This is true of both crystalline and CIGS, but the speed at which the efficiency drops as temperatures rise is faster for crystalline than CIGS.
“Eventually, those two curves intersect and the efficiency of a crystalline module drops below our efficiency,” Pimentel says. “This means that crystalline modules will then end up at a lower efficiency in real world conditions than our modules.”
RELATED: How new solar module technology lifts efficiency, limits price
What about the glut?
Forecasters warn of an upcoming module glut, an overcapacity that could bottom out prices and have a negative impact on module manufacturers. Will such a scenario bring us right back to the original problem, where thin-film loses out due to its lack of scale in an outsized market? Pimentel says Solar Frontier isn’t held hostage by the whims of the PV module market due in part to Showa Shell’s diverse energy interests, including its downstream investment in development pipelines around the world.
“We can focus our efforts on modules directly in markets where we can achieve greater margins where perhaps the Chinese and tier 2 have not made in roads, so they have no choice but to lower the price of their modules,” he says. “Showa Shell is an energy company that understands energy and manufacturing and is fully committed to the needed investment to bring our product to scale.”
— Solar Builder magazine
[source: http://solarbuildermag.com/featured/thin-film-pv-solar-modules-trending-up/]
Leave a Reply
You must be logged in to post a comment.