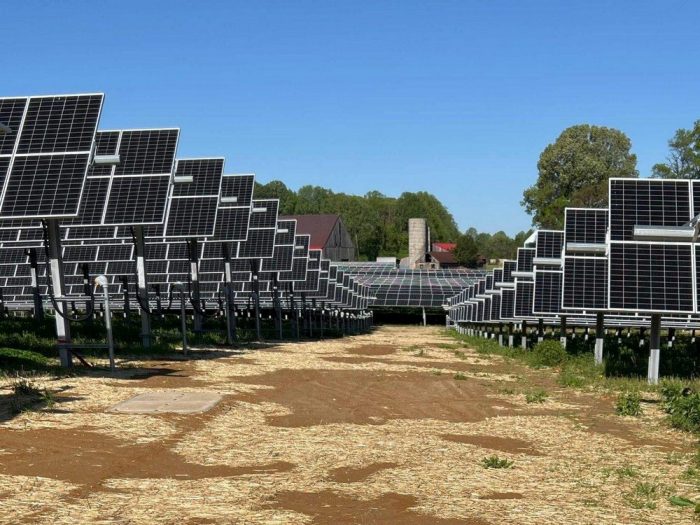
Protecting solar facilities from damaging weather can save project stakeholders big in the long run. A new report from VDE Americas and Wells Fargo Renewable Energy & Environmental Finance provides actionable strategies for the best way to stow trackers during a hail storm or other similar event.
Published Feb. 14, “Best Practices for Hail Stow of Single-Axis Tracker Mounted Solar Projects,” by Dr. Peter Bostock, VDE Americas; Ken Elser, Wells Fargo; and Jon Previtali, VDE Americas, provides guidelines for project stakeholders to prevent catastrophic hail losses on utility-scale solar project development activities.
According to GCube Renewable Insurance data, hail accounts for less than 2% of solar project insurance claims by volume — but more than 50% of total financial losses. The scale of these losses has disrupted the insurance market and hindered project development and financing. Calling for a collective and collaborative response, the authors of the report note that: “The solar sector is in urgent need of practical solutions to existential hail threat.”
“Hail has proven to be among the largest property damage risks for solar projects in hail-prone regions,” the report says. “Although property insurance and warranties play a crucial role in mitigating these risks, they do not eliminate the perils associated with severe hailstorms. Insurance often does not cover all exposure, and warranties are subject to carve-outs, photovoltaic (PV) module design standard limitations, and burden of proof. Where PV module hail resilience is insufficient on its own to reduce the risk of hail damage to acceptable levels in utility-scale projects deployed using single-axis trackers, project stakeholders must use defensive hail stow procedures to enhance system-level resiliency.”
The authors of the report say that stowing single-axis tracker-mounted PV modules at a maximum tilt angle reduces hail damage in two important ways:
- It can reduce the effective area of glass that is exposed to falling hail.
- It reduces the damage potential associated with hail impacts.
Horizontally oriented PV modules — aka 0° tilt or flat — are subject to the normal element of kinetic energy associated with falling hail. They’re taking direct blows. However, the report suggests that rotating PV modules to a tracker’s maximum tilt angle — about 50–75° — generally reduces the normal element of kinetic energy associated with falling hail, so that the modules are taking indirect or glancing blows, which significantly reduces the damage potential of hail impact.
With input from key stakeholders, the experts VDE Americas and Wells Fargo compiled several recommendations and best practices for hail alert and defensive stow protocols for single-axis tracker solar projects. The editors at Solar Builder have delved into the report to find the key takeaways for solar developers to help protect their projects from severe hail events.
1. Conduct an initial hail risk assessment for all projects. The goal of this initial assessment is to generally characterize hail risk (low, moderate, high) on a location-specific basis, as shown in Figure 1. For projects in hail-prone regions, engage a qualified party to conduct a science- and engineering-based hail loss study that covers time periods required by insurers (e.g., 500 years) and within typical investment hold periods (e.g., 10-, 20-, and 40-year hold). This hail loss study should provide probable maximum loss (PML) and average annual loss (AAL) estimates based on site-specific meteorological characteristics (e.g., historical hail event size and frequency) and project-specific technical considerations (e.g., primarily PV module glass thickness and strengthening, tracker maximum stow angle, and PV module size). Operators should use the results of this hail loss study to inform O&M procedures (such as stow protocols, hail stow alert trigger radius, and other operational criteria).
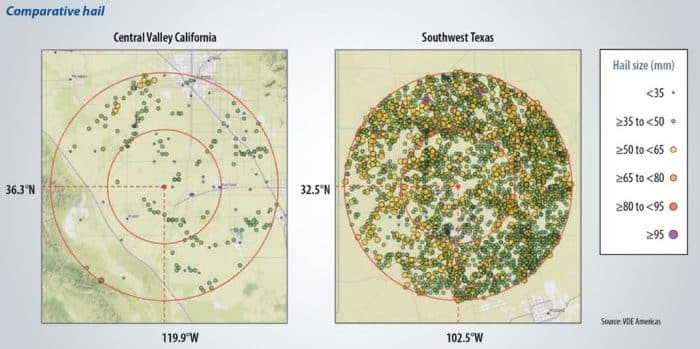
2. Automate defensive hail stow for operational projects based on alerts from a reputable weather service provider. This is typically accomplished by automated processing of electronic alerts or linking a frequent call response from an application programming interface (API) to the appropriate stow command via the project’s supervisory control and data acquisition (SCADA) system. Tracker manufacturers are starting to offer automated hail stow functionality natively and can typically support this functionality via custom hail alerting service and project SCADA system integration.
3. To optimize response times, projects should enable site-level hail stow functionality rather than stowing on a block-by-block basis. Some original equipment manufacturers may require that the project purchase optional services to enable effective, whole-plant hail stow.
4. A good default hail alert response is to stow PV modules at the nearest maximum tilt angle as quickly as possible. Avoid moving a tracker through a horizontal orientation (e.g., flat, 0° tilt) in advance of a fast-moving storm front without sufficient time to complete the operation, as this could inadvertently increase hail and wind damage.
5. Set trackers to a full hail stow position between dusk and dawn to minimize the overnight risk of hail damage. For trackers capable of withstanding full site wind speeds regardless of wind direction, face PV modules away from the prevailing hailstorm approach direction. Where hailstorms typically approach from the west (e.g., the CONUS), plant operating procedures should face PV modules to the east to minimize overnight hail risk.
6. To minimize the risk of hail damage before plant commissioning and energization, set trackers to a full hail stow position as soon as practicable during construction. For trackers capable of withstanding full site wind speeds regardless of wind direction, face PV modules away from the prevailing hailstorm approach direction. Where hailstorms typically approach from the west (e.g., the CONUS) construction contracts should generally call for facing PV modules to the east to minimize hail risk before the commercial operation date (COD).
7. In moderate to high hail risk locations, use targeted weather alert services to alert site managers and other personnel. Using such services as AccuWeather, DTN Storm Corridor, DTN Weather Sentry and others can provide site managers and remote operation control center (ROCC) personnel with proactive email and text alerts based on preset criteria. These alerts should be logged by the SCADA system for record keeping. Because email or text alerts may encounter delays, it is a best practice for the ROCC to automatically monitor relevant weather service alerts. Though regional weather forecasts are generally inappropriate for making project-level operating decisions, they may be useful for maintaining or heightening site readiness.
8. A good rule of thumb is to put trackers into hail stow if the National Weather Service predicts a severe thunderstorm. According to NOAA, a severe thunderstorm produces wind speeds greater than or equal to 58 mph and hail greater than or equal to 1 in. in diameter. When monitoring weather advisories, forecasts and broadcasts for a given site, note that severe hail can form in a variety of weather phenomena (e.g., supercells, high-precipitation supercells, multicell cluster storms, squall lines, mesoscale convective storms, elevated thunderstorms and tornadoes).
9. Use 1-in. hail events as a minimum remote alerting criterion. This is consistent with DTN’s “severe hail” alert setting. If weather service capabilities do not permit hail size differentiation, it may be prudent to use “any hail” (or a similar option) as a remote alerting criterion.
10. The radius for weather service alerts should be no less than 30 miles away from the project perimeter. In some cases, the radius should be up to 60 miles away from the project perimeter. To identify the optimal weather alert radius, evaluate the local meteorological conditions, the overall site hail risk, and the tracker response time to reach maximum tilt. A hailstorm can travel as fast as 60 mph and some trackers take 15 minutes or more to reach hail stow after receipt of the command.
11. Deploy one hail sensor or system for each square kilometer with spatial coverage across the full project footprint. For projects in moderate- to high-hail risk locations, permanently install hail sensors or systems to supplement the on-site meteorological measurements and weather alert services. The primary purpose of these on-site hail sensors or systems is to document site conditions during hail events for warranty and/or insurance claims. Sensors also are useful to assess the accuracy of weather alert services. Using on-site hail sensors to trigger an automated hail stow response is advisable only as a measure of last resort, as PV modules will already be incurring hail strikes by the time an on-site sensor triggers a defensive stow operation.
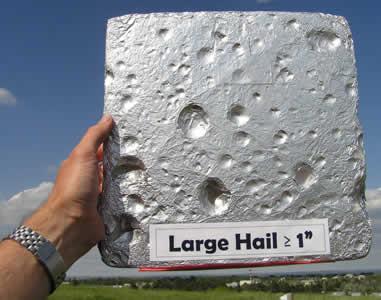
12. Consider using hail pads to corroborate hail damage. For projects using parametric insurance, where payouts are indexed to hailstone diameter, the use of a hail pad device can provide data on hailstone size distribution and mass. A hail pad usually consists of a Styrofoam panel covered by aluminum foil. Hail that strikes the pad leaves dents, as shown in Figure 2. A forensics expert can analyze these dents to characterize hailstone size and mass.
The entire report is available at the VDE Americas website.
— Solar Builder magazine
Leave a Reply
You must be logged in to post a comment.