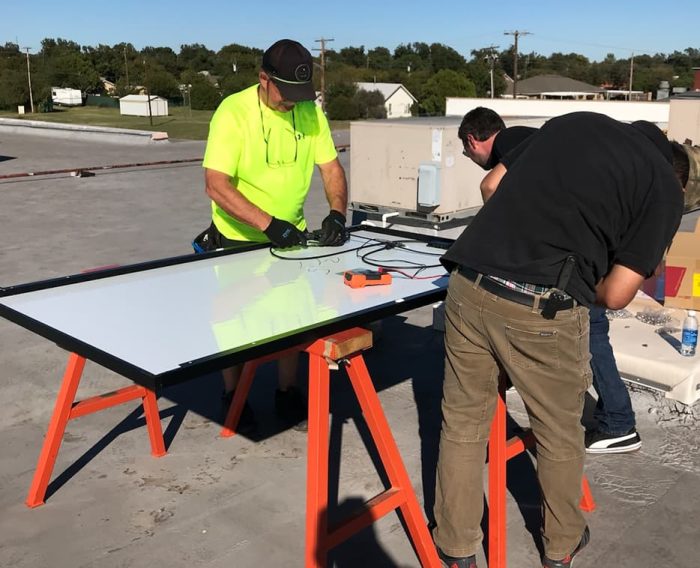
Contributed by Mark Gies, director and solar expert at S-5! | This month marks my 15th anniversary in the rooftop solar industry, my biggest stint in any single industry, by a longshot. Most of my solar career has been on the mechanical and structural sides of engineering, with mounting systems, application engineering, codes and standards, and all things where the rubber meets the road (or where solar meets the roof).
Recently, I have been thinking about common threads throughout my solar career and past career in product engineering in other industries. One of the most common questions that has chased me throughout my solar-racking career has been, ”What about wire management?” Years ago, I cringed every time I was asked; then somewhere along the way, I embraced it and invested a lot of research and time into educating and training others about wire management with the PV mounting systems I work with daily.
When I talk about wire management, I am only talking about what I call “under-module wire management.” That is specifically dc conductors, jumpers, MLPEs, ac trunk cables or any other items located underneath the modules in an array or sub-array. For me, the context has always been with rail-less solar, whether flat-roof ballasted racking during my years at PanelClaw or rail-less metal roof solar now at S-5!
Under-module wire management is tough to do efficiently; it has always been an afterthought but has a significant impact on time and money. Wires, MLPEs and other components need to be installed on the roof underneath (and sometimes attached to) the solar modules without touching the roof. These components are installed either before, during or after module installation. Tough to orchestrate, right? There are all kinds of clips, clamps, trays and other devices on the market, and plenty of installation techniques, but no silver bullet that solves all the problems.
Actually, the answer to that longstanding dreaded question about wire management is fairly simple: there is no “right” answer. The key is how you get to the “best” answer.
Design stage principles
Regardless of the products or techniques applied, my observation is the most critical step for a successful solar installation is at the project design stage, which happens long before you get to the job site. A project’s design has a huge impact on project costs, including under-module wire management. This is not rocket science, but from my prior career in other industries, I have found common issues and potential tools to help solar project designers drive down installation costs.
There is a popular discipline in product design called Design for Manufacturability and Assembly (DFMA), developed by Boothroyd and Dewhurst in the ‘70s, which introduced methods during the design phase to reduce final product costs. The main concept, which has been validated over and over again, is that more than 70% of the inherent product cost is finalized (and locked in) during design. That means after the design stage is complete, less than 30% of the costs can still be changed.
DFMA tools basically quantify qualitative manufacturing and assembly steps, creating a scorecard to benchmark designs, redesign them and re-score. This locks in product designs that are inherently low cost.
One example of the DFMA methodology is to map out the manufacturing steps and literally count hand movements and opportunities for mistakes for an assembled part, thus creating a scoring system that can be used to redesign and re-score to decrease costs. Another example is to score the number of components, so combination parts or pre-assembled parts score better, which drives the design and final cost in the right direction.
The concept and methods of DFMA are completely applicable to solar project design; let’s call this Design for Installation (DFI).
Design for installation
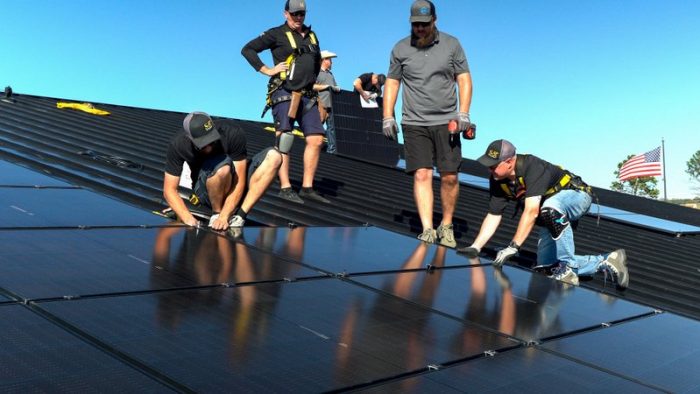
Clearly, a significant portion of time on the roof is “locked in” at the design stage, which means the design stage is the best time to design cost savings into the project, especially pertaining to under-module wire management.
The key is the designer must consider all pieces of the installation process in every aspect of the project design – from module prep to equipment pre-assembly and staging to the physical installation. Some processes should be viewed like a factory assembly line, where every second counts and needs to be repeatable and reproducible.
For wire management, by considering the installation up front, strings can be strategically designed, jumpers located, conductors clipped up or placed in trays and module conductors tucked up to minimize cost.
For module prep, designing exact conductor locations precisely where needed and clipping them securely to the frames will significantly impact time on the roof.
The overall concept is to design every component and its designated location to minimize wire lengths, wire tray lengths, reaching under modules, clipping jumpers under modules, etc.
Example: If a module layout consists of rows or columns of eight, specify string inverters of 16 modules. Then a string is one round-trip, and all the string-end conductors are easily accessible at the perimeters. Pretty simple, but not surprising that this may be overlooked if installation is not considered during project design.
Perhaps there is a need for DFI tools, methods, and scorecards specific to solar project design. These tools might prompt designers to consider the physical prepping and installation steps required during project design.
The key is to quantify the qualitative aspects of an installation, create a standardized scorecard, and then benchmark designs to drive improvements. No doubt this could have a big impact on effective under-module wire management.
I can envision methodologies of a weighted scoring system, such as adding the total length of jumper conductors or the distance from string ends to a perimeter module. Then the design process could be driven to improve the score. Or maybe count components, since every component must be brought up to the roof and installed or assembled in some fashion. Even a simple scoring system could be a big aid in better project design.
Regardless, any step a solar developer or installer can take upfront in the design phase to consider the installation steps would be worth it if costs can be reduced during installation.
Mark Gies is Director of Strategy and Market Development at S-5! Metal Roof Innovations. Mark is a mechanical engineer and business manager with 30 years of industry experience with a focus on solar.
— Solar Builder magazine
Leave a Reply
You must be logged in to post a comment.