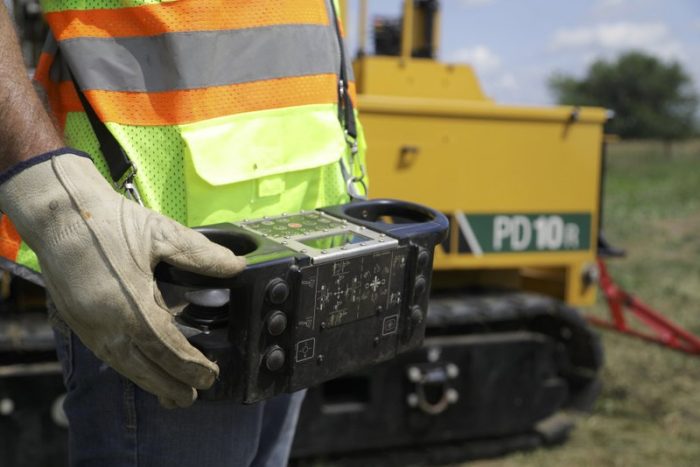
Pile drivers have become a go-to machine in the renewable energy market for the construction of ground-mount solar projects. As the construction of solar farms has grown exponentially in the last decade, contractors have begun looking for alternatives to the larger, traditional pile drivers. This has led to the development of a new segment of pile drivers designed for solar installation applications.
According to Ed Savage, product manager at Vermeer, solar contractors typically want to average 150 to 200 piles driven per day per machine — and large-scale solar farms can have hundreds of thousands of piles to be driven. This makes efficiency and accuracy so important because contractors don’t want to have to go back and redo anything. On installation projects of any scale, it’s about efficiency — the quicker they’re in and out, the better it is for overall productivity.
To respond to the market demand for pile drivers that can quickly and efficiently get this type of work done, manufacturers like Vermeer offer models that can do up to 15-foot (4.6-m) long piles, and others that can do up to 20-foot (6.1-m) long piles.
“Choosing the right Vermeer pile driver model will depend on how fast and how many piles a contractor wants to drive in a day,” finished Savage.
Considerations for choosing the right model
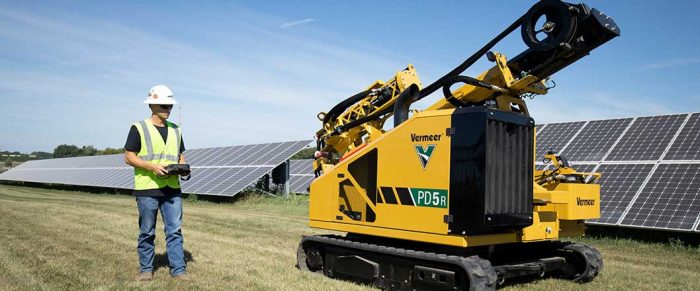
Project type makes a difference when choosing the right pile driver for the job. There are two basic types of ground mount solar projects, distributed (point-of-use) and utility-scale projects. If a contractor plans to focus on distributed projects, they would want to consider a compact unit with a light footprint to allow smaller transport vehicles.
“If a contractor plans to focus on utility scale projects, they may want to invest in a larger unit that can handle a larger range of pile sizes,” said Savage.
Another consideration is the mode of operation that best fits a contractor’s needs. Pile drivers are available as either a fully remote-operated machine or a manually operated machine. Some solar pile driver manufacturers may offer ride-on machines.
GPS-integrated pile drivers
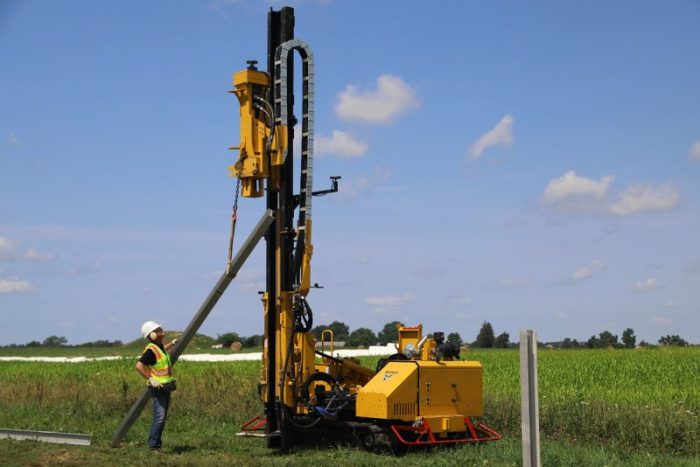
While most large-scale solar projects use pile drivers equipped with GPS for installing piles, not every machine integrates it to perform machine functions.
Pile drivers that do not integrate GPS with functionality require significant operator input to get piles aligned vertically and horizontally. In many cases, a laser is used to set up a string line to keep rows of piles aligned and maintain pile spacing. Then levels are used to check that the pile is plumb while being driven into the ground.
“It’s a time-consuming process and not efficient on large solar projects,” said Bo Howell, product specialist at Vermeer. “So, early on, when we developed our first pile driver, we worked with GPS technology experts to integrate information with machine functionality. Doing this allows pile drivers equipped with GPS to align piles vertically using the auto plumb feature.”
Automating the process
While GPS technology can significantly minimize the steps involved in driving piles on solar projects, new advances in machine automation technology help take things to another level. In 2022, Vermeer introduced the optional point-to-point (PTP) system for Vermeer PD10R pile drivers.
“The PTP system helps minimize the number of manual steps involved with positioning and aligning the pile driver on solar projects,” said Howell. “Throughout the course of a normal day, where many rows of piles are being installed, PTP technology can help operators maintain precise accuracy and work more efficiently.”
Automation point-to-point systems allow pile drivers to reposition themselves automatically using onboard GPS. After one pile is driven, the operator presses a button on the remote control, and the pile driver travels to the next coordinate and aligns to go to the next pile. Technology like this helps minimize the number of steps required from the operator during the pile driving process on solar construction projects.
“The pile driver can automatically perform seven machine functions that used to require manual input,” said Howell. “This helps keep operators and crews working efficiently and minimizes the number of laborers required to load piles throughout the process.”
Point-to-point systems allow a pile driver to automatically navigate to the next pile location, align the mast vertically and horizontally, then lower the hammer so the next pile can be lifted and loaded. The operator then raises the hammer with the push of a button and places the pile in the machine’s guide. From there, the push of a button engages the hammer floats. When the pile is at the desired height, the pile driver automatically starts and stops the hammer.
Once a pile is driven, a single button push raises the hammer, slides the mast away from the pile, moves the pile driver to the next pile site and lowers the hammer so the next pile can be loaded and lifted.
“During this repositioning time, operators still need to monitor the pile driver’s functionality, but they can also help get the next pile ready to be lifted. This can help minimize the number of people needed to support pile driving operations,” Howell explained.
Enlist help to select the right pile driver
Every contractor has different needs, which is why there is a range of models and technologies to choose from. To determine which is right for a company, Howell and Savage recommend working with a trusted equipment dealer.
Building the infrastructure of a solar farm requires a substantial amount of planning and development. Pile drivers are beneficial in these projects because they can accurately and efficiently place piles.
Madison Devin is a product marketing specialist with Vermeer Corporation based in Pella, Iowa.
— Solar Builder magazine
[source: https://solarbuildermag.com/news/innovations-in-pile-drivers-for-solar-projects/]
Leave a Reply
You must be logged in to post a comment.