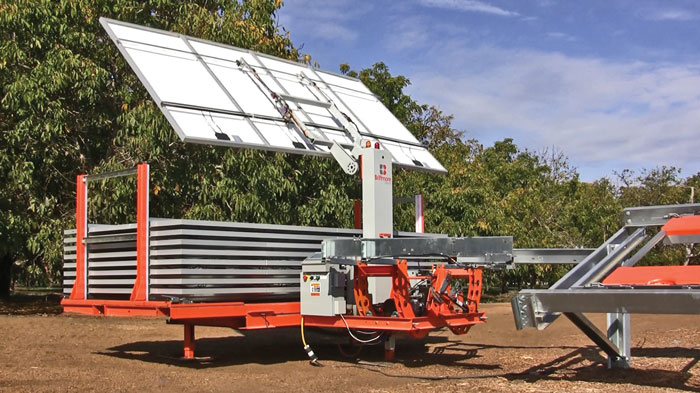
Brittmore’s automated installation can go at a pace of about 160 modules an hour.
Ever since the first solar PV system was installed, someone has been trying to remove components from it. Many of these are small and surgical — what used to need four bolts now needs two, what used to need clips no longer needs them — with each incremental reduction helping the bottom line, either in upfront costs or in time-savings.
The new utility-scale installation process developed by the Brittmore Group, on the other hand, approaches inefficiency with a sledgehammer instead of a scalpel. Using robotics, the California-based company has automated installation in such a way that less manual labor (the largest project soft cost) can accomplish twice as much, installing at a pace of more than 160 modules an hour.
“Say you use 30 heads for labor. We can complete the structural portion of that project in half the time,” says John Samuels, head of business development. “Or another way to look at it, if you have 30 heads, I could do the same job with 15 heads. If you look at the total project costs, everything — the SBOS, EBOS, modules, product management — we give an overall project savings of about 10 percent.”
Considering the potential ITC drop off, 10 percent could be the difference between a project sinking or coming together in 2017.
Here’s how it works
1. Prepanelization
Before we get to the magic of automation we have to start with some good old fashioned manual labor, but even here Brittmore has built-in efficiencies. Inside what Samuels calls the panelization assembly cell, or PAC, a team of workers assemble the modules into panels. Prepanelization isn’t necessarily new, but shipping large, prepanelized modules from the factory out to the field increases shipping costs that can reduce the intended advantages.
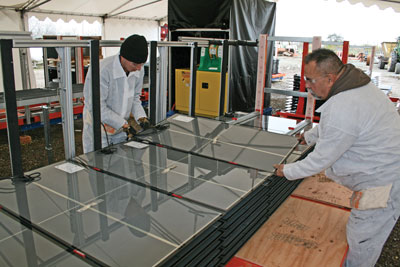
The panelization assembly cell in action.
Brittmore essentially constructs a tented, climate-controlled work station (the PAC) out on the jobsite in which workers take the individual modules and prewire them into panels. Since this is happening in the PAC instead of out in the field, the labor is less arduous and more ergonomic, and there are fewer electrical risks. Assembly of the PAC takes around 7.5 hours, and a staff is able to assemble over 40 panels an hour — the same pace of the installation machines out in the field.
2. Forklift
The assembled panels are now ready to head to the field. Workers stack the panels as they are completed onto a fixture, up to about 25 high (about 150 individual thin-film modules). The largest panel the system is equipped to handle is 2 by 4 meters. Those stacks are then driven out to the field where, yes, the magic finally happens.
“This process allows us to reduce the field labor needed to get the modules installed by transferring it to the PAC where it is much more ergonomically efficient,” Samuels says. “The fixtures are designed to allow safe transport of the panel stacks by protecting the individual modules.”
3. Robots
OK, enough of the manual labor stuff. The fresh stack of panels arrives at the start of a row where there sits a robotics system (there can be up to six of these on a single site). The fixture is placed onto the system, an arm comes down, grabs the top panel by the steel mounting rail, places it on the shuttle that is set into the racking, the whole thing shoots down the end of the row, the panel is placed on the racking and the shuttle zips back to do it again. All the while, the shuttle is mapping the route and knows how far to go on each pass and how many more panels will be needed to complete the row.
Meanwhile, a lone worker out in the field locks the panels down with a series of clips and hooks up the individual panels into their strings.
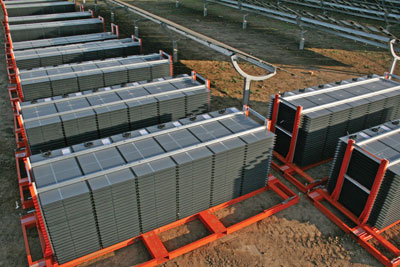
Stacks ready for the forklift.
4. Repeat
“When the fixture is empty, the robot contacts the PAC wirelessly and says, ‘I’m ready for more,’” Samuels says. “So you take the empty fixture out, put the new one in and it takes off automatically.”
From the PAC to the person plugging it all in, everything is seamless and operates more as a factory than a construction site: fewer workers all over the field; less demanding physical labor; fewer variables to account for; and more productivity. This all means reduced traffic in between the rows, which results in a cleaner end result, too — not a ton of dirt, mud and dust being kicked up onto the panels that then needs to be cleaned later.
RELATED: Mounting Challenges: Landfills, Brownfields, Water-Saturated Sites
What the system needs
Brittmore’s automated installation system is largely product agnostic. The company has its own racking system but can easily configure the shuttle to fit another racking systems.
Some systems may need to be simplified to accommodate the robotics, but requiring a reduced racking system also drives costs down further.
“We can change the pitch of our robotic systems so it can ride on the features of a different racking system,” Samuels says.
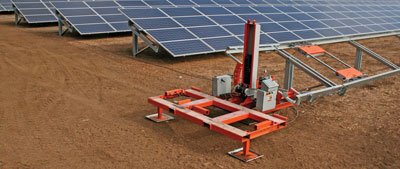
The autoloader and shuttle
According to feedback from the EPCs Brittmore has worked with, the biggest win might be how the system handles frameless modules. Part of the secret sauce is an adhesive back-bonding technology the team uses in the PAC instead of clips, which can be a pain when trying to mount and torque several modules in place.
“The industry is trying to get to frameless, but as you look beyond thin film and look at crystalline silicone — a 72-cell frameless module weighs a ton,” Samuels says. “Our robotics can handle it. The key is when you assemble the individual modules into a panel in the PAC, your guys are manipulating these heavy modules on a stable, flat ground, and then they mount them together using a galvanized steel back rail and silicone adhesive. The result is a very heavy and cumbersome panel that’s only being manipulated by robotics, not by people.”
The system does have its limitations. For one, the project site and size need to make sense.
“Due to deployment costs, we don’t do anything smaller than 2 MW,” he says. “Smaller than that and the deployment costs start to overwhelm the project costs.”
The system can handle only about a 10 percent grade in a site’s incline or decline, so a site with a steep or sharp hill could be problematic.
Row lengths are also a factor. The system can bridge gaps in rows, but if the site is more of a narrow configuration with a lot of short rows, some efficiency is lost due to constantly having to move robots around (the 40 panels/160 modules an hour measure is based on 200-meter long rows).
The system also works with fixed-tilt racking only at the moment, which limits some of Brittmore’s opportunities as trackers trend up. Samuels says a lot of the company’s business is on the East Coast right now because fixed-tilt is booming there, but Brittmore hasn’t ruled out a solution for trackers down the road.
“We are looking to partner with a single-axis tracker company that wishes to take advantage of our capabilities and make modifications to their tracker that allow us to work with it,” Samuels says.
Chris Crowell is the managing editor of Solar Builder.
[source: http://solarbuildermag.com/news/automated-solar-installation-robotic-technology/]
Leave a Reply
You must be logged in to post a comment.