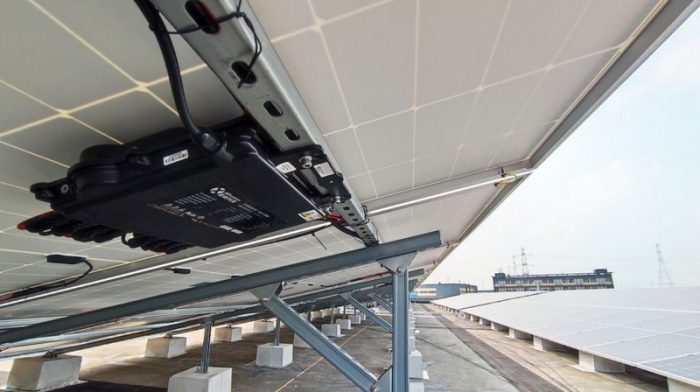
Technology is changing the norms of commercial and industrial (C&I) rooftop solar system design. Panels are getting huge and nearing 600 W. UL 3741 compliant systems are starting to hit the market to expand options for meeting NEC 690.12. And beefed up microinverters are poised to do in C&I what they’ve done for residential – simplify everything.
Wasn’t expecting that last one? Then it’s time to get up to speed on the advances made in microinverters built for C&I – many of which address the primary arguments made against microinverters in C&I to this point. In fact, let us address those right now.
Microinverters cost too much
Microinverters will likely still carry a higher price per Watt than a string-based system, but it is nowhere near the price delta that it used to be. Ten years ago this isn’t worth discussing, but now microinverter price per Watt has come down enough to narrow the gap to start the conversation especially after factoring in the extra equipment string designs often need to comply with rapid shutdown.
Microinverters are inherently compliant with rapid shutdown. From figures I’ve seen, for a 50 kW to 150 kW PV project, an RSS system could add another 50 to 70 percent to the cost of a string inverter depending on the products and the system size. Once you get close to a 200+ kW-size project, the string + RSS price point starts to provide more economies of scale and widen the gap again.
This doesn’t factor in any longer term system benefits either (we’re getting to that).
No shading, so no need
This is an understandable assumption, but microinverters aren’t just there to boost performance in shade. Do you have issues with dust or dirt or bird droppings? How often do you have someone go out and clean the panels? Keeping the whole array’s production elevated for a longer period of time between cleanings (being able to overcome dirtier panels for longer) is a benefit.
Back to the cost conversation. If microinverters can provide added production / require less panel cleaning maintenance, then the higher upfront costs could be mitigated by a lower levelized cost of energy (LCOE) over the system’s lifetime. Even if that CAPEX figure is 20 percent more, the production and O&M savings over time might make up for that delta.
More points of failure
Maybe? Depends on the microinverter, and if you’re factoring in additional RSS components of a string inverter system in comparison.
With a traditional microinverter, definitely, you’ll have 100 inverters for 100 panels. If you’re doing a string system with optimizers, that’s 100 devices — one for each panel — plus the string inverters.
But the big argument for microinverters in C&I is their ability handle up to four modules. If you’re installing 100 solar panels with multi-module microinverters that can handle up to four modules, you’re only installing 25 inverters.
The comparative points of failure are worth noting. A string inverter goes down, that could mean 100 modules go out at once. A microinverter fails, that could be one to four modules. With more micros vs. just the one string, of course, you do risk more individual panel outages here and there over time. Definitely another factor when doing that longer term LCOE comparison discussed earlier. Overall it could be a worthwhile O&M trade.
Just needing the 25 inverters also means 75 percent fewer units to purchase, stock, transport and install.
Microinverters are single-phase and a hassle to wire in three-phase
This is another area that was definitely a short-coming previously. Installers going with single-phase microinverters in C&I needed to balance the phases throughout the entire array. Doable, but a big headache. Here’s a diagram example:
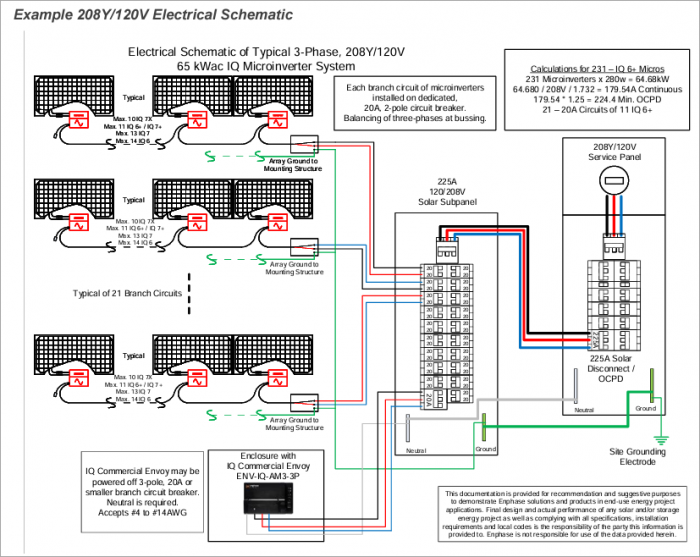
Re-training a staff to install microinverters in C&I just to deal with that complication doesn’t make sense. However, some advanced C&I microinverters now come in three-phase. Here’s an example of how that would look using a string of APsystem three-phase QT2s:
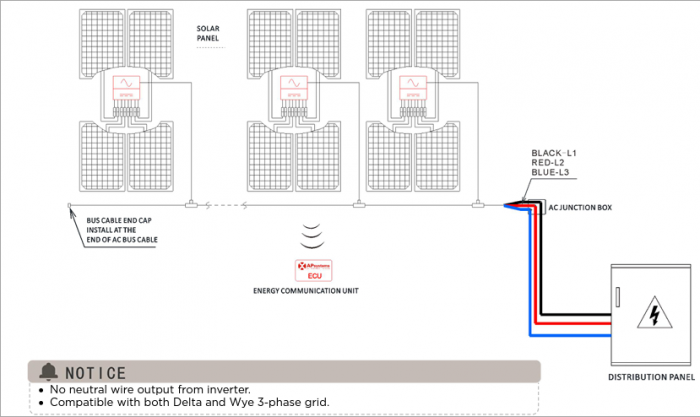
For an install crew that’s familiar with the plug and play nature of a microinverter installation, they can pretty easily scale right up to C&I rooftop jobs and not need to do any complex phase math.
Not powerful enough for higher Wattage modules
Again: maybe. Conventional single-phase microinverters can handle PV modules into the mid-300s, some newer models into mid-400s. The APsystems QT2 featured above can handle panels of 560 Watts (and higher, you’ll just need to match input voltage and current requirements — here is its data sheet.). Northern Electric Power (NEP) is another notable manufacturer with a line of microinverters for higher wattage modules on C&I sites.
Some other advantages to consider
- Flexibility. Whether it is a roof with varying angles, HVAC units that are in the way and shading parts of the array or other rooftop obstacles and awkward spacing, microinverters make design simple.
- No high voltage dc. This can be a safety concern at schools, hospitals, city center buildings depending on the city (not to mention installation crews). This is all ac.
- Some customers really like to have module-level monitoring.
- Stocking a similar product with all of the same accessories for both residential and C&I, if you want to focus solely on microinverters, could alleviate some headaches related to warehouse, logistics and training.
- Lender approval. In C&I, sometimes it just comes down to what’s on an approved vendor list (AVL) and what’s not, and more lenders are adding microinverters to their AVLs for commercial projects. Sunstone Credit recently added APsystems to its AVL.
— Solar Builder magazine
[source: https://solarbuildermag.com/news/making-the-case-for-microinverters-in-ci-solar/]
Leave a Reply
You must be logged in to post a comment.