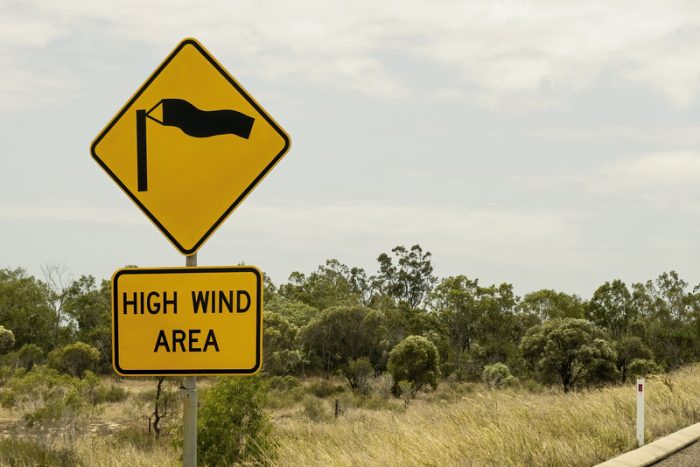
The solar industry — an emerging industry with rapidly evolving technology — is often, unfortunately, in learn-as-you-go mode. This is especially true when it comes to solar trackers, and understanding how they perform in various terrains and weather conditions. Traditional wind tests based on standard building codes often fail to capture the nuances of how different scenarios might affect a tracker’s design.
According to RWDI, a leader in wind tunnel testing, many important lessons were still being learned “just several years ago” for successfully designing solar trackers for wind resilience.
Trackers in the wind | Even though solar trackers are located low in the atmosphere, that is where wind turbulence is often at its highest levels, RWDI notes. Throw in the flexibility and mechanical movement of solar trackers, and they are structures that are especially prone to being excited by the wind—much more so than fixed-tilt installations.
In general, we already know that. Manufacturers have tested for and solved many issues related to static and dynamic wind forces and baked that into their structural engineering and tracker stow strategies. But RWDI believes there is still more to learn when it comes to “aeroelastic wind” forces.
Aeroelastic wind forces on solar trackers | Aeroelastic wind forces occur when an object interacts with the surrounding airflow in its environment. In the case of solar trackers, RWDI says aeroelastic effects—such as resonant vibration, torsional flutter, and torsional galloping—can cause the structures to vibrate or oscillate uncontrollably. This phenomenon is also known as aeroelastic instability. Explained further:
- Wake resonance is a phenomenon that occurs when two or more bodies move near each other and interact to create wave-like patterns that together form resonance, resulting in increased energy transfer between the two objects. In the case of solar arrays, wake resonance may generate turbulence from the first row of a solar array, which would then inflict resonant vibration on downwind rows.
- For tracker systems that utilize a central torque tube from a single location, a twisting form of vibration—or torsional flutter—can be initiated from the ends of a tracker.
- When structural stiffness is overcome at a critical wind speed, divergent oscillations— or torsional galloping—can occur.
Left unchecked, aeroelastic wind forces can lead to misalignment, reduced tracking accuracy, or component failure. Research into these effects opens up new opportunities for solar engineering advancement.
Aeroelastic remediation basics
To achieve an optimal, wind-resilient design for its new 1P TerraTrak tracker system, Terrasmart worked with RWDI to run multiple wind tunnel tests—totaling over 500 hours of testing. The methodology and results are published in a new whitepaper, “Mastering Wind: How to design and build optimized tracker systems that stand the test of time.”
The report notes these three remedial measures to account for aeroelastic wind forces:
- For resonant vibration: “Other than a structure’s natural frequency of vibration, variables such as wind speed, chord length, and damping play a key part in minimizing this aeroelastic effect.
- For torsional flutter: “Structural stiffness or damping are necessary to ensure that this effect is not experienced at expected wind speeds.”
- For torsional galloping: “Engineers can employ stow strategies at safer tilt angles or additional structural stiffness. Critical damping levels are required to mitigate this form of aeroelastic instability—making aeroelastic wind testing crucial to developing a high damping strategy.”
Engineering and/or procuring the right tracker system for a specific site, however, needs to strike the right balance between wing length, stiffness, and damping. This is why Terrasmart and RWDI conducted more detailed aeroelastic tests, in order to develop tracker solutions that meet regional weather requirements and withstand strong wind events.
Advanced aeroelastic testing and results
For this new approach to wind tunnel testing, Terrasmart and the RWDI team installed rotation and torque sensors on each row to quantify the instantaneous response and wind loading throughout the array as a function of time.
- Using both single-row and multi-row testing to account for all wind loading possibilities, Terrasmart engineers tested multiple wing lengths and damper configurations in a wind tunnel test to verify the effectiveness of a low-tilt stow strategy and determine which configurations work best to mitigate the negative effects of aeroelastic wind.
- Two viscous dampers of different strengths were tested separately and in combination with five different wing lengths between 20m and 80m, at three varying tilt angles. For each of the configurations, two wind directions were tested: winds normal to the tracker, and winds approaching from a 30-degree skew angle.
- The wind tunnel was increased to the next wind speed and the process was repeated until either the wind tunnel’s maximum speed was reached, or the dynamic rotations exceeded approximately 30 degrees at any location on the scale model.
The conclusion they came to in regard to aeroelastic forces:
“Our wind tunnel testing revealed that the lowest coefficient values were achieved with shorter wing lengths at low tilt angles. As the peak wind loads a 1P tracker can tolerate depend on different combinations of the structural elements, a key finding was that wing lengths between 30m and 40m were optimal and could maintain aerodynamic stability at high wind speeds.
“Determining peak stiffness and damping levels are also key to withstanding load deformation and mitigating aeroelastic instability. Although critical stiffness and damping setups are ideal, the right balance is needed to ensure cost-effectiveness and structural stability.”
Much more to master
The full “Mastering Wind: How to design and build optimized tracker systems that stand the test of time” report goes into much more detail on the wind tunnel testing overall, and explaining conclusions for optimal stow strategies for 1P vs. 2P trackers, testing for trackers in hurricane zones and more. Download it here.
Example of TeraTrak 1P in action
— Solar Builder magazine
Leave a Reply
You must be logged in to post a comment.