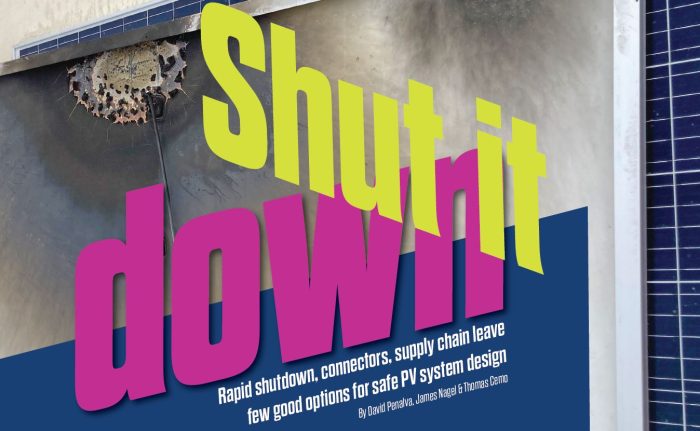
They say the best way to learn is by first making mistakes. Well, for most solar businesses, that might not be the best path to a higher education. Instead, let’s assess the mistakes that are commonly being made in PV system design and installations so that we can avoid them ahead of time. For our Q1 2023 NABCEP CE special issue, we reached out to a variety of experts and asked them simply: What’s going wrong?
In this piece, HelioVolta‘s David Penalva, James Nagel & Thomas Cemo show evidence of continuing safety issues related to rapid shutdown code and mismatched connectors — made worse by supply chain issues — and discuss some possible solutions.
Enter your email to check out the full 22-page What’s Going Wrong section in the digital edition that also covers structural flaws in trackers, the inadequacies of whole-home battery backup, large-scale underperformance and more.
Solar Builder Instant Access
Get instant access to the digital edition of Solar Builder magazine.
Shut it down
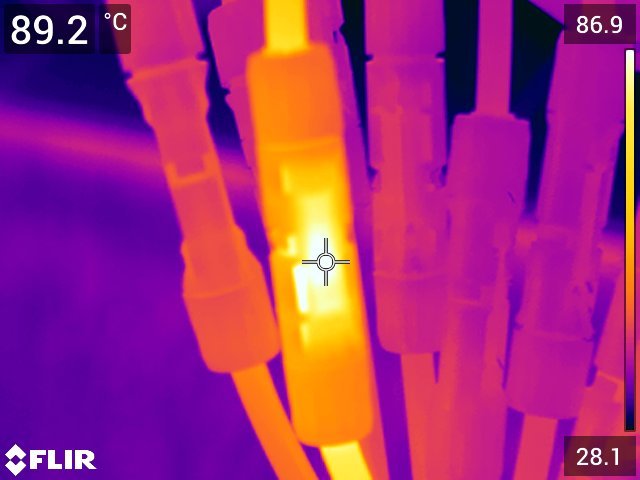
Solar PV components live in harsh environments with consistently elevated temperatures, thermal cycling and constant moisture. Moreover, module-level power electronics (MLPE) are more complicated electronics than PV modules. The increased use of these mass-produced power electronics components over the years has statistically added more failure points to U.S. rooftop solar systems. More failures mean more thermal events.
While some stories about fires are public, many are not, so it is hard to gauge how prevalent the failures are. However, system owners and hosts are taking these risks seriously and taking appropriate measures to mitigate said risks. The cost of a thermal event far outweighs the cost of safe equipment, third-party inspections and retrofits.
We will discuss the issues and possible solutions in this article. But first, how did we get here?
Background
In an effort to create safer situations for first responders on the roof, the National Electric Code (NEC) has undergone several evolutions through the years. Starting with NEC 2014, new requirements were introduced to address the issue of dc voltage present even when systems are shut off. One of the major changes in the 2014 code was the introduction of a 10 ft array boundary, which required no additional equipment if the inverters could be kept within that zone. However, for all dc conductors outside of the 10 ft boundary, additional equipment, such as pass through disconnects, were required.
In 2017, the NEC upped the requirement to a 1 ft boundary, requiring additional equipment to be used. The industry did not have optimal solutions for this requirement at the time but had to react to the code changes. The only solution for this was the use of MLPE.
The changes in the NEC code had a significant impact on the inverter market and the way systems were designed and installed. Inverter market share in residential solar shifted significantly from string inverters to MLPE-based systems (microinverters and optimizers) from 2013 to 2019, according to the Wood Mackenzie PV Leaderboard.
As we face another upcoming code change, it is time to pause and question whether the requirements we’ve implemented thus far are actually accomplishing their mission.
One point of concern is whether 80 V is actually a safe voltage. OSHA defines 50 mA as a potentially lethal current, which can happen at 80 V depending on the current path through broken skin. Given that firefighters are also wearing a significant amount of personal protective equipment (PPE), this is very unlikely. So, while it is true 80 V is safer, the benefit is questionable after factoring in 1) firefighter PPE and 2) the additional failure points introduced by the rapid shutdown components themselves.
Rapid shutdown failures
Rapid shutdown system components can cause thermal events, thereby making systems less safe, resulting in a higher frequency of needing firefighters on site. Simultaneously, news media reports of thermal events possibly related to rapid shutdown devices (RSD) and PV connectors have increased.
At HelioVolta, as a third-party auditor, we have seen evidence of this in our system health assessments. The photos throughout this article are just a small sample of problems we commonly see.
Connector issues are common and still plague the industry. Even good intentions, like the jumpers seen here, still miss the mark.
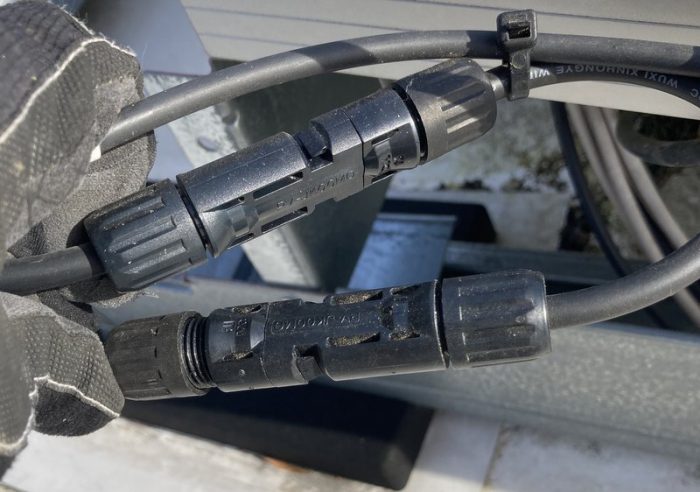
Human error is a factor that must be considered, even if the right components are used. Cross mated connectors can introduce incompatibility between tolerances and material. Over time, the mismatch can grow to a hot spot that can only be identified with a thermal camera (as seen earlier).
Even when connectors are not cross mated, the use of factory-made jumpers from multiple vendors, introduces varying levels of quality control (QC) and makes traceability in the event of a failure for warranty claims incredibly difficult. This is common on large utility-scale projects utilizing pre-assembled whips and harnesses and multiple sub-contractors.
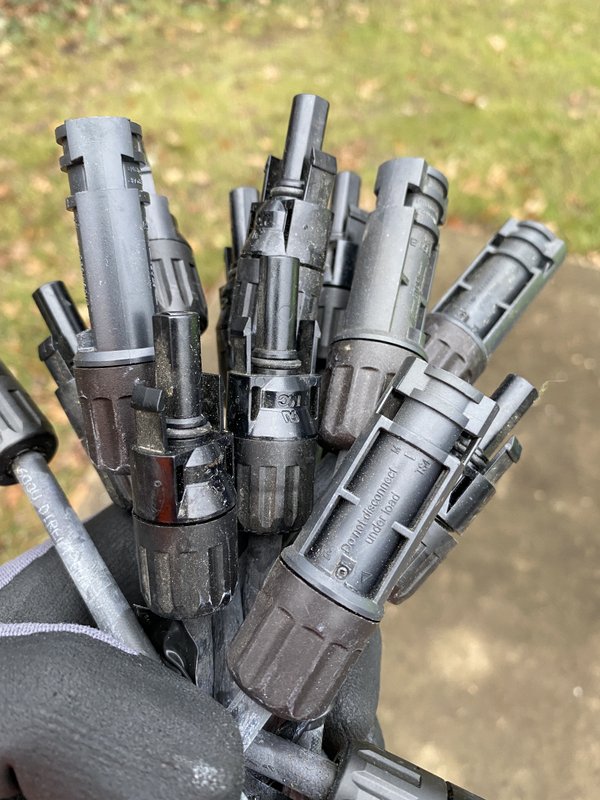
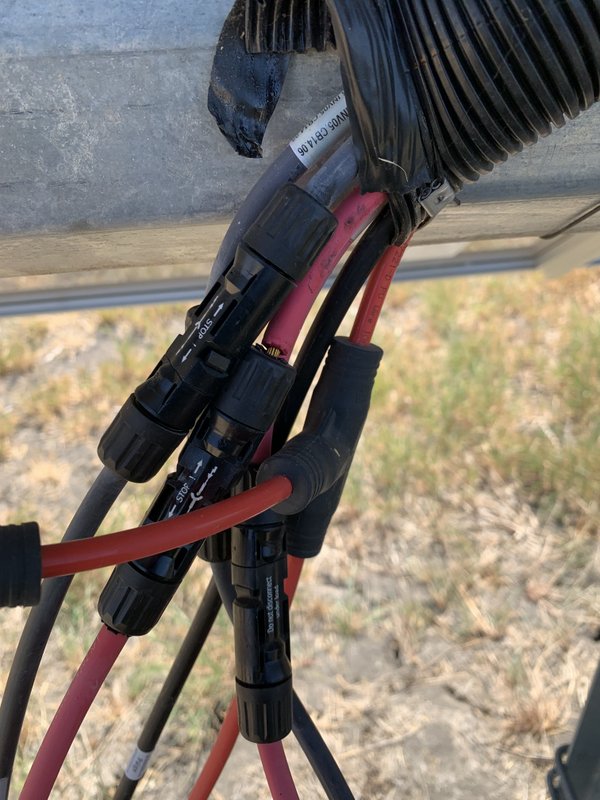
Occasionally, a failed connector is found during a health assessment inspection, like the one below, and is extremely troubling because it presents the immediate risk of an open circuit condition near the rooftop membrane, as well as the long-term risk of possibly hundreds more like it on the same rooftop.
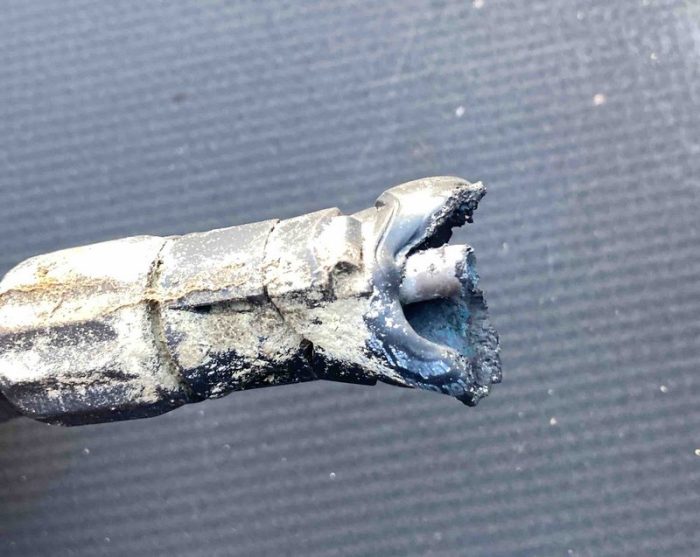
We’ve seen a dramatic increase in stakeholders taking connector issues seriously and working to implement changes. However, failures in rapid shutdown devices are still relatively new and not well understood by many. We’ve had the opportunity to investigate several incidents and better understand the nuances and challenges faced during installation. The photo below shows how the thermal deformation of an RSD caused by overheating can be very subtle and almost indistinguishable. However, when it progresses to the point of failure, it can be catastrophic.
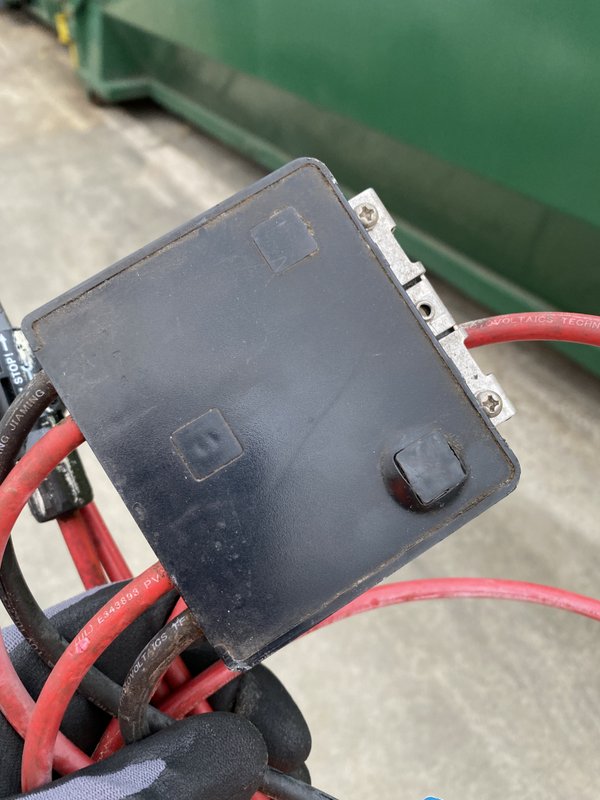
The burn marks on this module provide some evidence to postulate how the components failed. The exact mechanism of the failure is still unknown and being investigated, however the evidence of the power electronics failing cannot be ignored.
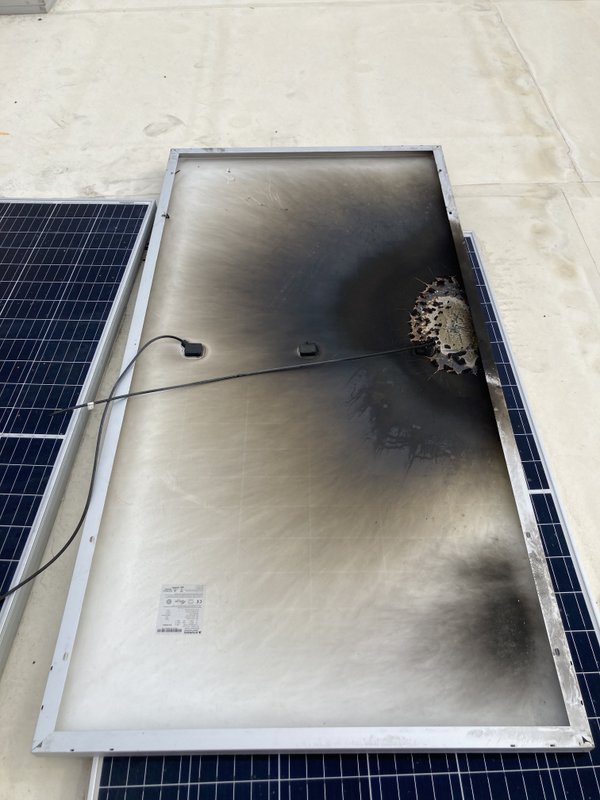
The risk is well-understood by owners and system hosts and emphasis is placed on identifying failing components, poor workmanship or incompatible equipment.
New risks emerge
The ongoing supply chain difficulties plaguing the solar industry compound the issue at hand. Many times, preferred products or modules are not available, and installers do not know what they will receive until it arrives on site or have to accept what is available. This forces the hand of installers to either wait for the preferred equipment or figure out alternative solutions to get the job completed on time. Typically, projects cannot wait.
This also exacerbates the most common issue to this point: mismatched PV connectors from the module to the rapid shutdown device. The 2020 NEC code cycle took this into account by requiring “like connectors,” which will solves the cross-mating problem — but it may create another.
To mitigate potential connector failures from cross-mating, one solution is to use factory-assembled jumpers to ensure like connectors are mated. However, adding jumpers only increases the number of connectors, which then doubles or triples the potential failure points.
Using factory rather than field-assembled jumpers is a smart solution because it reduces the variability of making connections on the roof with the wrong tools or inadequate training. However, choosing the right jumper supplier is also a key detail to consider. A “factory-assembled” jumper is often still being manufactured by hand on an assembly line and not by an automated process. This lack of automation can also lead to inconsistent quality control, which can vary from company to company, so jumpers must be purchased from a reputable supplier with strong and reliable QC standards.
The combination of 1) more complicated equipment in the system, 2) increased connection points, and 3) heavy pressure to keep installed costs low is a perfect recipe for disaster, and it is a recipe we have baked into the code. Solutions must be evaluated thoroughly with a high consideration to operational longevity.
Solutions?
Better planning during the design and procurement stage, preventing this from becoming an actual problem. This means the engineering and procurement teams need to work closely to specify the components that have to interact with other components to confirm that they are in fact compatible and available. This step seems obvious but is often overlooked or not emphasized. It is a challenging process due to the market dynamics and supply chain constraints coupled with accelerated design schedules. However, it is critical to avoid more complex technical solutions (like jumpers), which add more points of failure.
Improve system monitoring practices and response times. It typically takes a few days to go from the first warning signs to an actual thermal event. Improving the criteria for alarms related to warning signs can help reduce the risk of fire. Additionally, improving response time once early warning signs are detected is also a key factor. The challenge with this solution is relying more heavily on O&M providers that are monitoring hundreds or thousands of systems simultaneously and the inherent inertia of changing engrained business practices.
Consider UL 3741 certified equipment that provides a path to eliminate MLPE. The new certification has its own pros and cons when compared to current solutions. For example, when a system is contiguous, and the inverter can be placed within the array boundary, with certain UL 3741 certified systems, MLPE is not necessary, thus eliminating additional components and connections. However, due to the recent publication of the standard, there are currently few solutions in the market that have been certified.
Current rapid shutdown solutions still have their place with large, distributed arrays when a contiguous design is not possible. However, this evolution in the code and industry provides an opportunity to revisit safety provisions originally proposed by rapid shutdown requirements.
Global examples
The issues we face in the U.S. are not unique. Other countries also face similar challenges. One example is the dc isolator requirement on rooftop systems in Australia that was introduced in 2012 to make systems safer. However, the equipment was prone to water intrusion and often led to fires when the dc contacts were submerged. Fire and Rescue New South Whales’ statistics showed solar PV related fires increased five-fold in the ensuing five years, many attributed to failing dc isolator switches.
The requirement was eventually dropped in late 2021. This highlights the importance of understanding the potential risks and unintended consequences that come with new standards and regulations.
The solar industry is finding itself in a predicament where following the code that is intended to make PV systems safer statistically adds risk. The industry cannot rely on MLPE as the sole solution for rooftop systems. Alternate options are required to provide safe and reliable systems that can last their expected 25-year lifespan and deliver on the promises made. UL 3741 is a step in the right direction, providing flexibility in design options.
David Peñalva is CEO and co-founder of HelioVolta. He has an engineering background leading technical teams with more than 15 years of experience in the solar and energy storage industries.
James Nagel is COO and co-founder of HelioVolta. His degree is in mechanical engineering with a PE in electrical engineering with more than 10 years of experience in the solar and energy storage industries.
Thomas Cemo is the engineering services manager at HelioVolta. He has an engineering background, a master’s in mechanical engineering, and over 10 years of experience in the solar industry.
HelioVolta is a solar and energy storage software and technical advisory services company. Their SolarGrade platform standardizes solar and energy storage inspection procedures, enables team collaboration and generates shareable professional reports. Contact them at hello@solargrade.io.
— Solar Builder magazine
Leave a Reply
You must be logged in to post a comment.