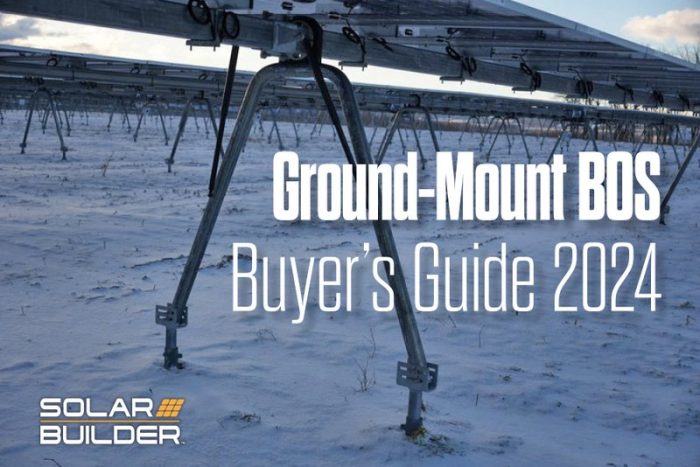
As part of the Solar Builder 2024 Ground-Mount Solar BOS Buyer’s Guide, we asked solar electrical balance of system (solar eBOS) suppliers questions regarding trends in solar tracker design and utility-scale solar sites – and how those impact cable and wire management as well as other solar eBOS considerations. Here are their responses.
Does the trend of “terrain-following” solar trackers cause any wire management or other solar BOS headaches?
Transition point terror | “Terrain following racking can cause nightmares for wire management. Tracker manufacturers often need to add knuckles/joints, table gaps or motors on these rows, requiring additional and careful consideration for your wire management strategy. We refer to these as ‘transition points’ that can also include areas where you are transitioning from a fixed point to a moving point (tracker to disconnect or Cable Messenger System), or from moving areas to other moving areas. Almost always in these transition areas, you need to have a robust wire management solution called an arrest point to prevent damage to the cable and prevent catastrophic wire management failures. Additionally, a polymer solution is almost always recommended due to the extreme movement that can happen in these areas.” – Nick Korth, product marketing manager, HellermannTyton.
Structural reinforcement | “One of the biggest challenges facing the solar industry is land use. With ‘easy’, flat and expansive land for development appearing fewer and farther between, solar project sites with meaningful terrain variance are becoming the norm. However, developing on these sites invariably creates headaches for developers and EPCs. Trackers have a tendency to be unstable when installed on undulating ground causing a range of issues, from unsettled and leaning piles, to cable issues which can be known to occur due to movements in the structure. Often our dedicated solar technical team will work with clients’ engineering teams to understand the situation, site and engineering requirements before sharing our recommended solution.” – Dean Barlow, Group Solar Product Manager at Gripple.
Example: Gripple’s Solar Bracing Kits can help to prevent this unwanted movement in tracker piles on slopes.
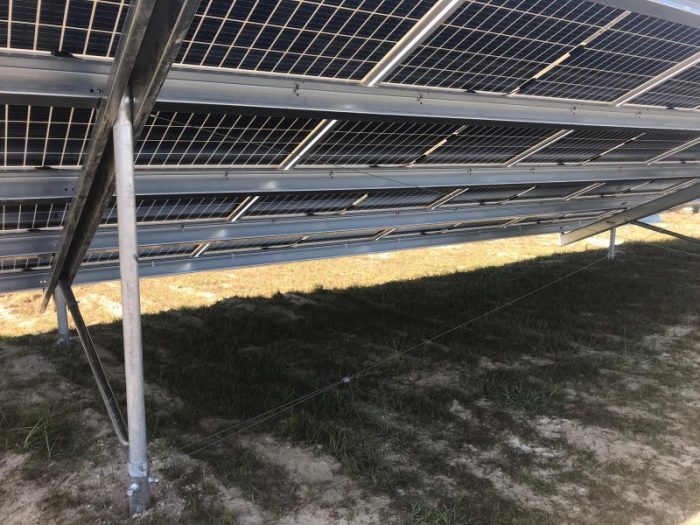
The Solar Bracing Kits have a two-way locking device known as a PV Dynamic Tensioner that allows you to install a brace quickly and easily between two piles. Applying pre-tension using a fast and unique tensioning tool, the PV Bracing Kit will ensure the frame stays rigid, eliminating misalignment that might occur due to external forces and environmental loads. The ready-to-use kits are fast and lightweight, drastically improving health and safety on-site.
What should EPCs consider in terms of “sustainability” when selecting mounting and cable management?
Avoiding waste | “Repeat visits for PV wire-management problems are an incredible waste of resources. Look for solar mounting systems with an integrated wire-management plan from the moment the PV wires leave the module,” – Patrick Wylie Jr, Infinity Rack.
Virtues of metal | “The largest determinant of sustainability in cable management systems (CMS) is durability – will the system last the life of the project? Many of the plastic solutions that have dominated the solar industry for decades ultimately do not pass this test. Plastic products are problematic as UV and heat exposure degrades them at a rapid pace. When the plastic degrades, the product may not be able to provide reliable support for the cables. However, metal wire management components, if engineered appropriately, will last the lifetime of the plant even in the most extreme weather conditions. Metal solutions outperform plastic wire management products when we consider embedded emissions and compatibility with the circular economy.” – Scott Rand, CEO and Co-Founder, Affordable Wire Management.
Product lifetime | “I view sustainability as the most cost-efficient aspect over the life of the system. Plastic or metal, you want a part that, once installed, won’t damage cable that would potentially need to be replaced. You should also be careful not to choose inferior-grade polymer-based solutions that will fail prematurely, requiring multiple replacements. Additionally, the sourcing of the parts is crucial,” – Korth, HellermannTyton.
Domestic content | Products that are manufactured domestically not only benefit from the IRA’s domestic content tax adder but also reduce shipping costs and emissions.
Example: Solar Snake Tray Max XL
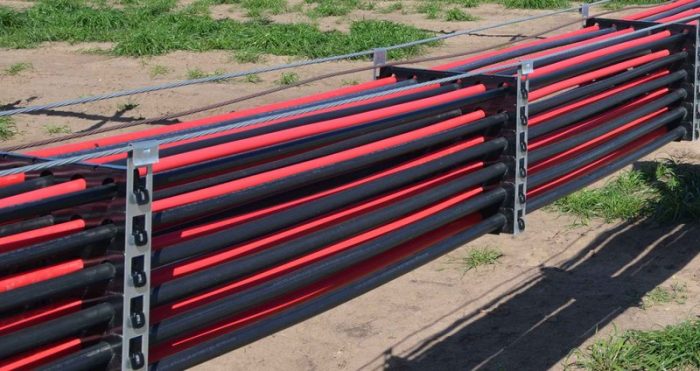
Snake Tray products are all manufactured in the United States. The Solar Snake Max XL manages cables ranging from 350 Kcmil up to 1250 Kcmil from the module to the interconnection area. This trenchless solution installs as fast as 22,000 feet in a day offering a safer, less labor-intensive solution. The open-air design maintains NEC 310.15 compliant cable separation which allows the cables to operate more efficiently to yield up to 30-watt hours per meter far surpassing that of bundled cables. The above ground design also allows for easy installation, operation and maintenance.
What’s an innovation or new partnership that will meaningfully speed up large-scale solar installation times and reduce labor costs?
Above ground CMS | “In many global markets, suspending solar PV cables above ground has become a preferred cable management method. Above ground routing mitigates many issues associated with trenching, including difficult terrain, poor ground conditions, historic land use or flooding,” – Barlow, Gripple.
Quickly avoid cable sag | “Installation of cable management systems (CMS) is a time intensive process on many utility-scale solar projects. Above-ground messenger cable systems have historically required construction crews to manually tighten and install the messenger cable at each individual pile – a process that can take days. Improper installation of the messenger cable can lead to cable snap, which is highly dangerous, or excessive cable sag which causes a plethora of challenges during the operation of a solar power plant.” –Rand, AWM.
Example: AWM developed its PHOTON Toolkit to decrease cable sag. It has improved installation rates by 2.5 times or more in some cases.
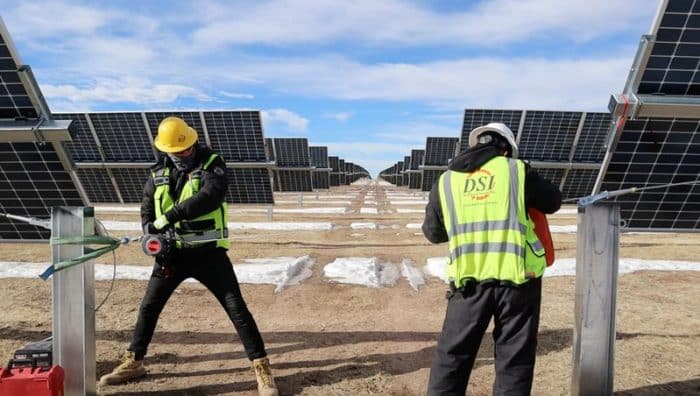
Increasing the efficiency of the AWM CMS installation frees up valuable work hours for onsite crews, allowing them to meet tight deadlines. The AWM team also reviews and looks for areas to contribute value engineering, such as optimal cable routing to reduce CapEx and improve site access. AWM’s CMS provides opportunities to reduce cable size, resulting in documented cost reductions as high as 80% of the CMS.
“The labor costs associated with eBOS and wire management are well known but not discussed enough. Significant amounts of often monotonous labor go into installing parts that can be easily misapplied. That’s why one of our team’s core focuses is to engineer all products to be as safe, efficient and installer friendly as possible. We do this through proprietary product designs that resonate from automotive assembly lines in Detroit all the way to solar farms in Lancaster, California. We develop parts that reduce manual labor and eliminate user error, like our new Nextracker and ATI Ratchet Clamps.” – Korth, HellermannTyton.
Example: Over the past year, HellermannTyton has been compiling best practices of many different applications, which culminated in the recent launch of its Golden Row Kit program. Customers that discuss eBOS in early phases of utility-scale projects receive more of a consultative approach to wire management.
— Solar Builder magazine
[source: https://solarbuildermag.com/news/solar-ebos-insight-terrain-following-sustainability-trends/]
Leave a Reply
You must be logged in to post a comment.