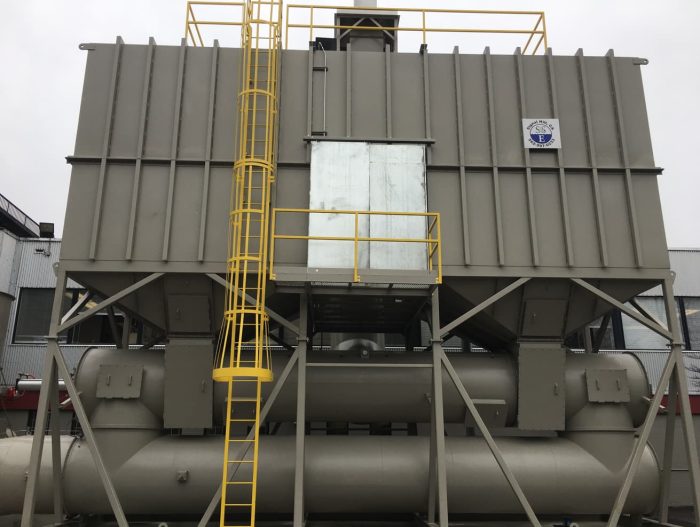
Renewable energy isn’t inherently “green” or “clean.” Solar energy is generated from products that are mass produced in factories that have their own carbon footprints and environmental pros and cons that vary depending on the facility, company and/or country or state of origin.
Ship & Shore Environmental (S&SE), a pioneer in clean air technologies, has been readying systems geared toward solar facilities in preparation for the upcoming post-Inflation-Reduction-Act (IRA) U.S. solar manufacturing boom.
“Reshoring of PV panel production presents an incredible opportunity for the U.S. and its manufacturers to lead the world by example,” says Anoosheh Oskouian, CEO of Ship & Shore Environmental. “There are so many environmental and financial incentives for companies to develop and implement cost-effective pollution abatement solutions in their manufacturing. Cleaner production now will also help make future solar panel recycling safer and more affordable.”
S&SE is in talks with a handful of solar assembly facilities right now and offers a host of services around pollution abatement, including consultation, customized engineering, design, fabrication and on-site deployment of new and retrofit equipment.
For solar specifically, regenerative thermal oxidizers (RTOs) are commonly used. S&SE oxidizers excel in the capture and/or treatment of the various chemicals and VOCs inherent to the manufacturing of all types of solar panels.
PV with minimal VOCs
The PV panel assembly process involves thin films, light glass materials and silicone-based materials, all of which must be chemically coated. Some of the potentially hazardous chemicals used in solar panel manufacturing, if not handled properly, include cadmium and lead, as well as volatile organic chemicals (VOCs), such as various alcohols, silicones, acetates and hydrochloric acid, among others.
“Whether they use thin films, whether they go with glass material or silicon-based materials, they need chemical coatings in order for it to be able to sustain,” Oskouian says. “Without proper treatment, the waste from fabrication of solar panels would otherwise go to landfills.”
The coatings are really where VOCs come into play, which is what Ship & Shore seeks to eliminate. “This stuff is lighter than air and some of the chemicals are potentially deadly. Inhaling just a small amount could cause serious problems,” Oskouian says.
VOCs are also hugely problematic for the environment and populations beyond the facility if unregulated.
“Some of the facilities that we had looked at have multiple layers of coating that is applied for strengthening and for conductivity,” she says. “So, depending on what the application is, the end result would create all of that exhaust from various applications to go out of a chimney.”
Controlling chemical air pollution means collecting from areas where the chemicals are directly applied on top of any surfaces (i.e., the coating area, where glue is applied, a drying oven) as well as the post-production staging area where products give off “fugitives.”
Oskouian says they “capture all of that from a direct source inside. On the outside, we build enclosures around the area to collect VOCs that are in the air.”
The VOCs are sucked through ducts and piping and then destructed in a process of combustion with heat, that is generated “by everything that we have collected.”
The end result of Ship & Shore’s process is water vapor, CO2 and the destruction of 98 to 99% of all VOCs collected. Secondly, after controlling for VOC pollution, Ship & Shore designs systems to provide heat recovery — capturing heat energy from the plant and reusing it.
Of nations and regulations
Often the extent of what S&SE can do — or how readily a solution is adopted — comes down to state regulations of emissions allowed from a facility.
California, which has the most stringent air pollution rules in the country, is referred to as 10-ton area — 10 tons is the maximum a facility can send out. So, thinking back to the 98 to 99% VOC destruction — “basically, that 2% of the overall emissions can go out and they will stay below the allowable levels,” Oskouian explains. Texas is a surprisingly close second with between 10-25 tons/year.
A lot of solar panel manufacturing takes place in the Midwest and Southeast. Ohio, for example, just follows federal EPA guidelines. The EPA guidelines are driven by regions (there are 13), population density of these regions, and whether they are considered attainment or nonattainment. Rural areas with less population density have higher allowable limits. The maximum allowable emissions is capped at 100 tons/year.
The IRA, in addition to its solar manufacturing incentives, also includes incentives for installing pollution-reducing equipment at these facilities. The law targets any U.S. organization that “re-equips an industrial or manufacturing facility with equipment designed to reduce greenhouse gas emissions by at least 20% through the installation of … energy efficiency and reduction in waste from industrial processes, or any other industrial technology designed to reduce greenhouse gas emissions, as determined by the Secretary, or which re-equips, expands, or establishes an industrial facility for the processing, refining, or recycling of critical materials.”
In other words, companies that install equipment to clean up their renewable energy waste processes stand to benefit.
“Regulations around waste have not caught up to demand and volume in solar panel manufacturing,” Oskouian says. “This is the time for manufacturers to provide what the market and world needs from this clean energy sector, and with proper pollution abatement, they can deliver the panels needed for this clean energy in a way that is healthier, more forward-looking, and more likely to qualify for federal incentives.”
End of life impact
According to EPA guidelines, some solar panels are considered hazardous waste (depending on the leachability of RCRA toxic materials present in the solar panel). PV panels should be recycled — a process that involves more facilities with their own emissions and eco considerations. Oskouian’s team is readying a solution for these facilities too.
“They have to worry about the materials that were used, and the chemicals that were used in the process upon breaking it down or smelting it,” she explains. “They will have to address what would be coming off of this [recycling] plant.”
The more onerous air quality regulations often result in a less harmful final product overall, which helps at end of life.
“The panels we’ve evaluated in the U.S. have a lot more alcohol of different types instead of more harmful materials like cyanide or hydrochloric acid,” she notes. “But if we are also recycling panels that were made outside the U.S. without our domestic manufacturing regulations in mind, they may have larger amounts of the more toxic, harmful chemicals.”
Oskouian believes all of this reinforces the importance of U.S. solar panel manufacturing and onshoring as much as possible, beyond the political aims of jobs and localization.
“We all get very excited about this,” she says, “and I am 100% behind keeping manufacturing in the U.S. and becoming the strong industrial country that we used to be as long as we do it with an environmentally conscious mind and address some of the issues at hand that need to be really paid attention to.”
Chris Crowell is the Editor-in-Chief of Solar Builder.
— Solar Builder magazine
Leave a Reply
You must be logged in to post a comment.