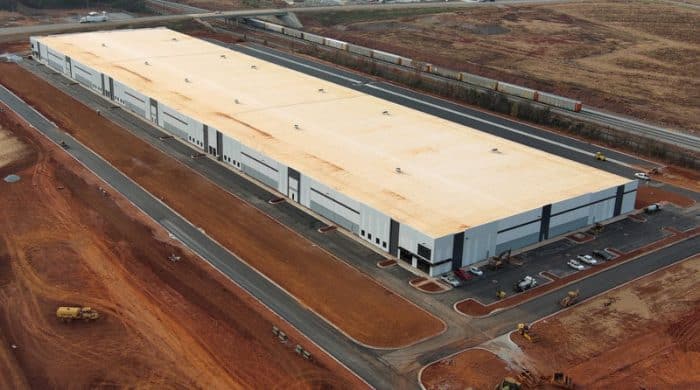
The solar tracker manufacturing market in the United States has seen rapid growth over the past year and a half thanks to tax incentives within the Inflation Reduction Act (IRA). A domestic content bonus within the law was meant to encourage more U.S. manufacturing to bolster the solar supply chain.
“The domestic content bonus under the Inflation Reduction Act will boost American manufacturing, including in iron and steel, so America’s workers and companies continue to benefit from President Biden’s Investing in America agenda,” said Secretary of the Treasury Janet L. Yellen in May 2023.
The domestic content adder in the IRA included tracker components like torque tubes and structural fasteners. In November 2023, Treasury and the IRS issued its long-awaited guidelines for the tax credit, confirming that eligibility will be determined by a “substantial transformation” test, meaning eligible products must be substantially transformed at a U.S. factory to be considered for the credit.
There are two eligibility tests for the adder: One for steel and iron, and another for manufactured products:
- Under the steel and iron test, 100% of the structural steel in new projects must be U.S.-made.
- The manufactured product test requires that 40% of the cost of manufactured products must be from U.S.-made products. The percentage increases by 5% each year for projects that start construction in 2025 and after, maxing out at 55%.
Fixed-tilt systems fall under the 100% steel and iron test. Trackers are considered a manufactured product and fall under the second test. (Read more about that in more depth here.)
While the math gets tricky on how to earn the domestic content tax credit, there’s no question that the incentive has driven U.S. solar tracker manufacturing since the IRA was passed in 2022.
RE+ in September 2023 seemed to be a flashpoint for the expanding domestic solar tracker market, with the announcement of numerous new and expanding production facilities to boost the U.S. supply chain for the solar market. The industry has seen several tracker manufacturers partnering with solar module manufacturers and steel suppliers to expand production and juice up their domestic content percentages. Here is a recap.
OMCO Solar opens sixth U.S. plant in partnership with First Solar
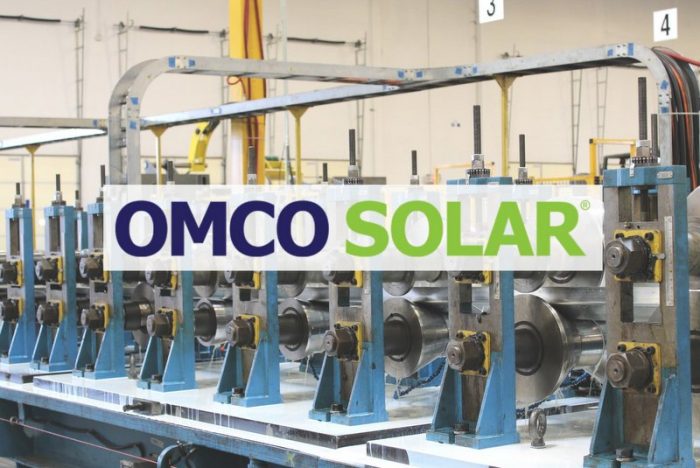
OMCO Solar and First Solar, two U.S.-based manufacturers that have worked closely together over the years, announced a new manufacturing partnership in September 2023. OMCO Solar, which will start to manufacture steel backrails for First Solar’s upcoming Series 7 modules. In conjunction with the agreement, OMCO opened its sixth U.S. manufacturing facility in Alabama to facilitate the First Solar deal.
To scale quickly and support the expected Series 7 volumes, OMCO’s new plant will be near First Solar’s own manufacturing facility in Lawrence County, Alabama. OMCO Solar invested $10 million in what will be its second plant in Alabama, which will encompass approximately 201,000 sq ft and will bolster the company’s overall manufacturing capacity to over 10 GW across its six facilities.
Domestic manufacturing has always been part of OMCO’s mission, said Eric Goodwin, director of business development for OMCO Solar, in a Q&A with Solar Builder at Intersolar North America 2024. OMCO started in the solar industry as a contract manufacturer, putting its steel roll-forming capabilities to work for other solar tracker suppliers. The company then started to manufacture its own solar products via a “factory-direct” model in 2017.
“We’re ahead of the curve on domestic steel,” Goodwin adds. “That has always been our business model from Day 1. As much as the IRA has brought the industry a lot of momentum and a lot of excitement, one of the intents is to bring more jobs and more manufacturing to the U.S. I think it gives us an opportunity to continue to grow, but I think equally important, as we make things in the U.S., is that our products are good quality.”
First Solar already has an advantage in terms of its percentage of domestic content vs. other global module brands, and the steel backrail produced at OMCO’s Alabama plant will only add to that lead. Meanwhile, OMCO will continue to work strategically with existing partners to bring utility-scale trackers to market in 2024.
The company is inching closer to manufacturing the entirety of its tracker in the U.S.
“At the moment, there are only three parts of the tracker that we don’t make in-house, in the U.S.,” says Matt Kesler, director of solar technology for OMCO Solar. “We’re looking at strategies for all of those parts, as well. If there is somebody that’s going to be able to make an entirely 100% U.S. tracker, we might be able to be the first to do that.”
Goodwin adds that having a strong domestic content percentage in its products could mean the difference between getting a contract or not.
“There are many customers that have become well educated and have tax attorneys, and they want to know what can we do,” he says. “You have customers that are even mixing modules on a site to get to that 40%. I think that it varies on many projects, depending on what the developer is looking at, that it could be a win or loss type scenario.”
Nextracker unveils new contract manufacturing lines
Nextracker has been steadily inking contracts for more domestic tracker production since early 2022. In September 2023, the company unveiled its newest dedicated manufacturing lines in Las Vegas in partnership with Unimacts.
The new facility will produce critical steel components exclusively for Nextracker to use in ground-mount solar plants to serve projects in Nevada and Southwestern states.
“With the Nextracker dedicated line, we will be supporting gigawatts of utility-scale projects annually, powering homes and businesses across the Southwest and even as far east as Indiana and Kentucky,” said Unimacts CEO Matt Arnold.
In April 2022, Nextracker announced a deal with JM Steel for a dedicated production line to manufacture solar tracker components. The facility with JM Steel is on the campus of the Steel Dynamics Inc. (SDI) facility near Corpus Christi, Texas. The production line will provide multi-GWs of solar tracker capacity annually.
Announced prior the passage of the IRA, the deal was aimed at controlling volatile steel pricing and increasing U.S.-based sources for the solar industry. The 97,000 square-foot JM Steel Sinton facility opened in October 2021 and represents a $40 million investment.
“JM Steel’s proximity to SDI will provide Nextracker and their customers cost-effective products with quick response times to feed the growing solar market in Texas and the South,” said Tony Calandra, CEO of JM Steel. “And all of the steel being used to make Nextracker’s products will be made with SDI’s newest Electric Arc Furnace (EAF) technology, which utilizes recycled or scrap steel as a raw material for a lower carbon footprint which is a perfect fit for Nextracker’s solar products.”
Nextracker has added more than 25 GW of annual domestic solar tracker capacity with dedicated production lines announced in Texas, Arizona, Pennsylvania, Illinois, Tennessee and Nevada.
Array Technologies expands deals with key production partners

Array Technologies announced two agreements in September 2023 to expand its domestic tracker production.
The first was a nearly $35 million investment with Belding, Michigan-based Extruded Aluminum Corp. (EAC). The two companies strengthened their 10-year partnership with a deal to expand Array’s U.S. manufacturing footprint with additional aluminum extrusion capacity to foster sustainable domestic supply.
“Our relationship with EAC enhances our industry-leading capability to source in excess of 85% domestic content, the highest percentage in our sector,” said Kevin Hostetler, CEO of Array. “This strategic alliance not only elevates the dependability of our supply chain but also offers our customers a reduced risk profile. By focusing on proven U.S. manufacturers like EAC, we can enhance on-time delivery and exceptional quality, supporting our clients in meeting stringent Inflation Reduction Act (IRA) requirements.”
This long-term collaboration supports EAC’s nearly $35 million capital expansion, which includes adding 180,000 square feet to their existing facility and the addition of one of the largest aluminum presses in Michigan. The new press will expand the aluminum extrusion possibilities for EAC’s customers and enable further design innovation for Array’s products.
“Our alignment in sustainable business practices, as well as our contribution to Array’s ever-strengthening U.S. supply chain, reflects our shared goals of industry leadership and commitment to renewable energy,” said Charlie Hall, CEO of EAC.
The second deal Array announced in September was with Fort Wayne, Indiana-based Steel Dynamics to provide a fixed supply of steel coil for Array’s U.S. projects. Steel Dynamics will source the coil from its flat roll steel mills located in Indiana, Mississippi, and Texas.
“Array’s collaboration with Steel Dynamics is a powerful affirmation of our dedication to a robust and flexible domestic supply chain,” Hostetler said, mirroring what he said about the EAC deal.
This strategic partnership allows Array to expand its domestic content offerings, further reducing risks for its customers. Array’s flexibility in its supply chain allows the Array tracker to have more than 85% U.S. sourced material, making it easier for customers to meet domestic content requirements in the Inflation Reduction Act (IRA).
Priefert Steel manufacturing Nevados trackers
Priefert Steel has begun manufacturing Nevados’ all-terrain solar mounting and tracking equipment at the Priefert factory in Mount Pleasant, two-and-a-half hours east of Dallas. Priefert says this new line of business is due in part to the IRA.
“We’re proud of our factory with 23 acres under one roof, and our focus on high-precision steel manufacturing,” said Rocky Christenberry, Priefert’s Vice President of Manufacturing. “The Nevados focus on design innovation in all-terrain trackers makes us great natural partners.”
“Domestic supply chains can be both more robust and more efficient, such as by reducing shipping times and associated carbon emissions and pollution,” said Yezin Taha, founder and CEO of Nevados. Buying as much domestic equipment as is available now helps prepare solar developers for a future when more U.S. solar module capacity has come online, Taha said, making high percentages of domestic content and the bonus tax credits more achievable.
In addition to launching this factory, Nevados has continued to expand its client base in the United States. By the close of 2023, Nevados will have contracted for enough trackers to supply about 1.5 gigawatts of solar generating capacity in the US, with both existing and new strategic client partners.
Bradley Kramer is managing editor of Solar Builder.
— Solar Builder magazine
Leave a Reply
You must be logged in to post a comment.